Hydro Inc. has a strong engineering capability and an expansive global reach in the pump industry, especially in aftermarket services. Pump Engineer had the pleasure of speaking with George Harris, Chief Executive Officer and Founder of Hydro Inc., where he discussed the company’s recent research initiatives, reliability support for customers, customized designs and the significance of upgrades and health audits.
Written by: Deirdre Morgan
Publisher: Pump Engineer / December 2016
“We were very fortunate that early in the company’s development we had the good fortune to work closely with Dr. Elemer Makay, a foremost consultant to the power generation industry and a specialist in troubleshooting multi-stage, high energy pumps”, states Harris. “Engineering combined with meticulous observation and analysis in the field were key to his troubleshooting process. As a result of his training over a twenty year period, engineering became the focus and strength of Hydro Inc.’s aftermarket services”.
According to Hydraulic Institute statistics, 85% of the critical pumps in industries, such as power, refineries and pipelines, are custom designed for the specific application intended. In order to properly rebuild, upgrade or troubleshoot these installations requires a solid aftermarket engineering capability and experience. Not only must the engineer understand pump fundamentals, but also the application and system in which the pump is being used, as well as the changes that may have occurred in plant operating conditions since the pump was originally installed.
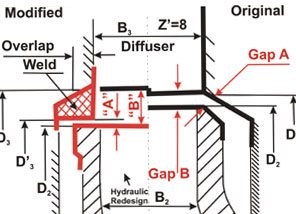
A&B gap design.
Many engineered pumps were designed to last the lifetime of the plant. However, changes in plant operations have occurred over time which can affect the reliability, performance and efficiency of the pump. Understanding these changes are critical to a successful repair or upgrade project. In essence, engineering is at the heart of all that Hydro Inc. does.
Hydro Inc. is one of the only pump aftermarket companies with both a strong engineering capability and a global footprint. Typically, aftermarket services have been controlled by the pump OEMs with a broad range of capabilities and resources. At the other end of the spectrum are small local machine shops which are able to turn around a repair quickly, but may lack pump specific engineering skill and engineering support.
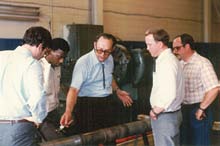
Dr. Elemer Makay shared his engineering knowledge with Hydro’s engineers.
Hydro Inc. is unusual in that it is an independent company with the capabilities of the OEMs, but retains its small company heart with a commitment to agile and responsive service. “We believe we
are among the best in the industry in mobilizing people and resources to respond to the emergencies that can befall even the best managed plant. Our primary industries include power generation, including nuclear, oil and gas, and steel, but we are capable of servicing almost any industry using custom engineered pumps”, says Harris.
Hydro Inc. works on a range of products from a broad spectrum of OEMs, yet, it is a challenge to hire and/or develop staff that can work in this custom engineering environment. Like in many industries, while the company has a diverse staff with a wide range of experience, the pool of experienced people has been reduced. They have therefore developed in-house training programs and have created a unique
Engineering Manual specifically for the aftermarket. “We have been building the programs and systems for sharing engineering experience, technical information and best practices among all of our service centers and their staff”, adds Harris.
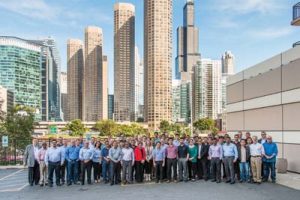
Hydro global engineers.
Research & development
Hydro Inc. has consistently been an early adopter of new technologies, including the use of CNC tools in an aftermarket service center; state of the art balancing equipment; stationary and portable coordinate measuring equipment and scanners; 3D modeling software and 3D sand printing. “The innovative process we have pioneered for the pump industry enables us to provide critical cast parts, such as impellers, on an expedited time frame of 2 – 4 weeks in most cases, significantly less than typical industry lead times”, states Harris.
Through their test lab in Chicago, which is certified by the Hydraulic Institute, they have participated in research projects with customers and with universities, including void fraction testing for the nuclear industry; testing of new milled vane impeller technology; development and testing of new impeller designs; analyzing vibrations; and performance problems for pumps up to 5500 HP. As an independent lab, the test lab is often used in developing data to troubleshoot and research a range of pump problems.
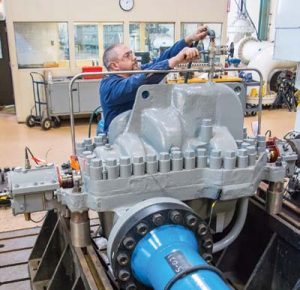
Hydro Performance Test Lab.
Harris further details some of the milestones that Hydro Inc. has recently achieved: “We are very proud of some recent accomplishments, including the certification of our test lab by the Hydraulic Institute and being awarded a long term contract for a key oil account in the Middle East region, where we will support all of their pump aftermarket needs for the next 10 years. We are also proud of the new design, manufacture and testing of a vertical pump for a nuclear power plant. This code pump was the first of 14 pumps included in the multi-year contract”.
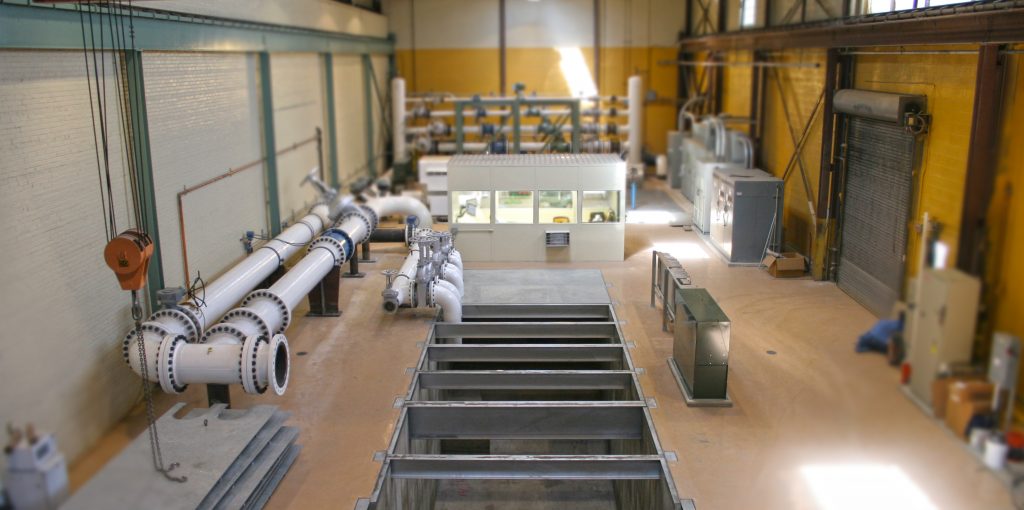
Hydro Performance Test Lab – Certified by Hydraulic Institute.

Hydro Reliability Service in-field testing.
Repair is an opportunity for improvement
Hydro Inc. places a great importance on improving a pump’s performance and in turn, prolonging a pump’s life span. Harris explains that taking the time to review the current operating condition in relation to the pump’s original design specifications can lead to engineering recommendations for improving a pump’s performance and extending its life. A thorough inspection process and report provides the framework for analyzing what caused performance to deteriorate or, in the case of a failure, what caused the pump or pump component to fail, also creating an opportunity for recommendations to correct problems. “A visit to the site, a review of the pump’s history and on occasion a pump test – either a health audit in the field or a full pump test in the test lab – provide critical information for the engineer’s review. Hydro Inc. undertakes three major categories of upgrades, which are mechanical upgrades, material upgrades and hydraulic modifications”, says Harris. He continues on to explain what each upgrade entails:
Mechanical upgrades
“Mechanical upgrades can be performed to reduce vibration, increase bearing and seal life, and to reduce power consumption. Pump engineers review the pump’s design, check the existing geometry and make recommendations to change any of the variables, which can affect a pump’s strength and ability to meet performance requirements”.
Material upgrades
“The engineering team will evaluate the metallurgy of your pump’s components and recommend upgrades specific to your application. Material upgrades can improve a pump’s ability to withstand corrosive or erosive effects of the liquid being pumped; improve a pump’s tensile strength and prevent premature failure; improve a pump’s performance through reduced running clearances; and prevent pump seizures during run dry events. In addition to traditional metals, a range of composite materials is available, each of which address specific issues”.
Hydraulic modifications
“Hydro Inc. uses advanced hydraulic design tools to analyze a pump’s performance and can tailor a new impeller design to meet a plant’s current requirements. As Hydro Inc. customizes the design specifically to a plant’s current needs, the new design can translate into significant improved efficiency, reduced energy costs and enhanced reliability. In manufacturing the new impellers, Hydro Inc. employs the latest patternless casting methods to produce a high quality casting with dimensional accuracy and a quality surface finish. To ensure that the new impeller meets all of the plant’s requirements, the pump with its new impeller can be tested in the test lab and a detailed test report produced. To achieve the best result, the latest technology is supported by expert engineering every step of the way in an upgrade or re-rate project”.

Hydro Engineers reviewing parts design.
Applying the practices
Recently, Hydro Inc. had the opportunity to put these practices to use in a nuclear power plant. The plant was experiencing repeated issues with a bank of 10 pumps in a service water application. A number of factors were involved in the problems being experienced with these pumps. Problems included design issues; poor quality manufacturing; a corrosive environment; packing box leakage corroding the foundation, as well as inefficiency of the existing design in the current operating conditions. When a decision was made to build a custom designed pump, Hydro Inc. brought to bear its engineering experience and current day technologies to develop and manufacture a new design which addressed all of the complex issues being experienced. “In this particular instance, upgrades included hydraulic improvement, optimizing wear ring geometry and high quality casting processes, which ensured dimensional accuracy and smooth surface finishes. Assembly processes were optimized and the packing box was redesigned for a seal-less construction. This complex project involved hydraulic design, mechanical, structural and metallurgical upgrades”, says Harris.
Diagnostic technology optimizes performance
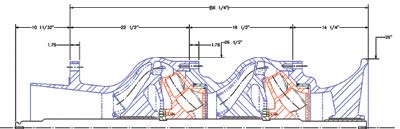
Hydraulic Design of Pump Critical Dimension in 2D.
Focused on ensuring reliability for end user rotating machinery, Hydro Inc.’s pump improvement engineers work with on-site maintenance and engineering staff to provide reliability support for pumps, whether the equipment has been installed for years or has only been recently commissioned.
A very important part of maintaining a healthy fleet of pumping equipment is investing in periodic testing. This cost effective tool affords the opportunity to better understand the hydraulic and mechanical health of the pump and the driver. The health audit typically includes collection of data and an evaluation of the equipment in the following areas:
- Hydraulic performance
- Pump and driver vibration analysis
- Opportunities to proactively apply predictive maintenance
- Electrical motor assessment
- Identification of opportunities to improve operating and maintenance practices
“These tests can be performed either before or after equipment overhaul to help maintenance staff plan and prioritize for equipment down-time as opposed to running to failure”.
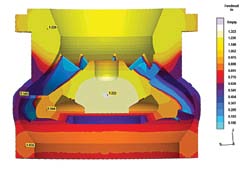
Analysis of Mold Design Using Solidification Simulation.
See more at – pumpengineer.net