Testing Services
for Vertical, Horizontal,
and Submersible Pumps
Key Features Include:
- Certified Hydraulic Institute (HI) test lab in compliance with HI testing standards, e.g. 14.6 and 40.6
- API 610 testing standards on applicable pumps, including variable speed testing
- Capable of testing horizontal, vertical, and submersible pumps
- Flow capacities up to 42,000 gpm
- Horsepower capacity of 5000 HP
- Multiple Variable Frequency Drives, including Siemens 5000 HP 2300-4160 V drive
- State-of-the-art data collection systems for hydraulic performance, vibration, temperature, power, etc.
Designed for the
Pump Aftermarket
The Test Lab is designed in compliance with Hydraulic Institute Standards and API 610. It’s capable of testing horizontal, vertical, and submersible pumps up to 5,000 HP. With pump testing at Hydro, Inc.’s Test Lab, customers can improve reliability, reduce unforeseen costs, and prevent pump failures.
Energy Savings
The rising cost of electrical power has caused many industrial plants to shift their focus to energy efficiency. Plants often run pumping equipment continuously, and much research has pointed to opportunities for cost savings by optimizing pumping equipment.
When evaluating the potential for energy savings, end users cannot consider a pump in isolation. The suitability of the pump for the system within which it operates is vital. Even the best designed and most efficient equipment offers power-saving potential if it is run off its best efficiency point (BEP) in a system for which it is ill-applied.
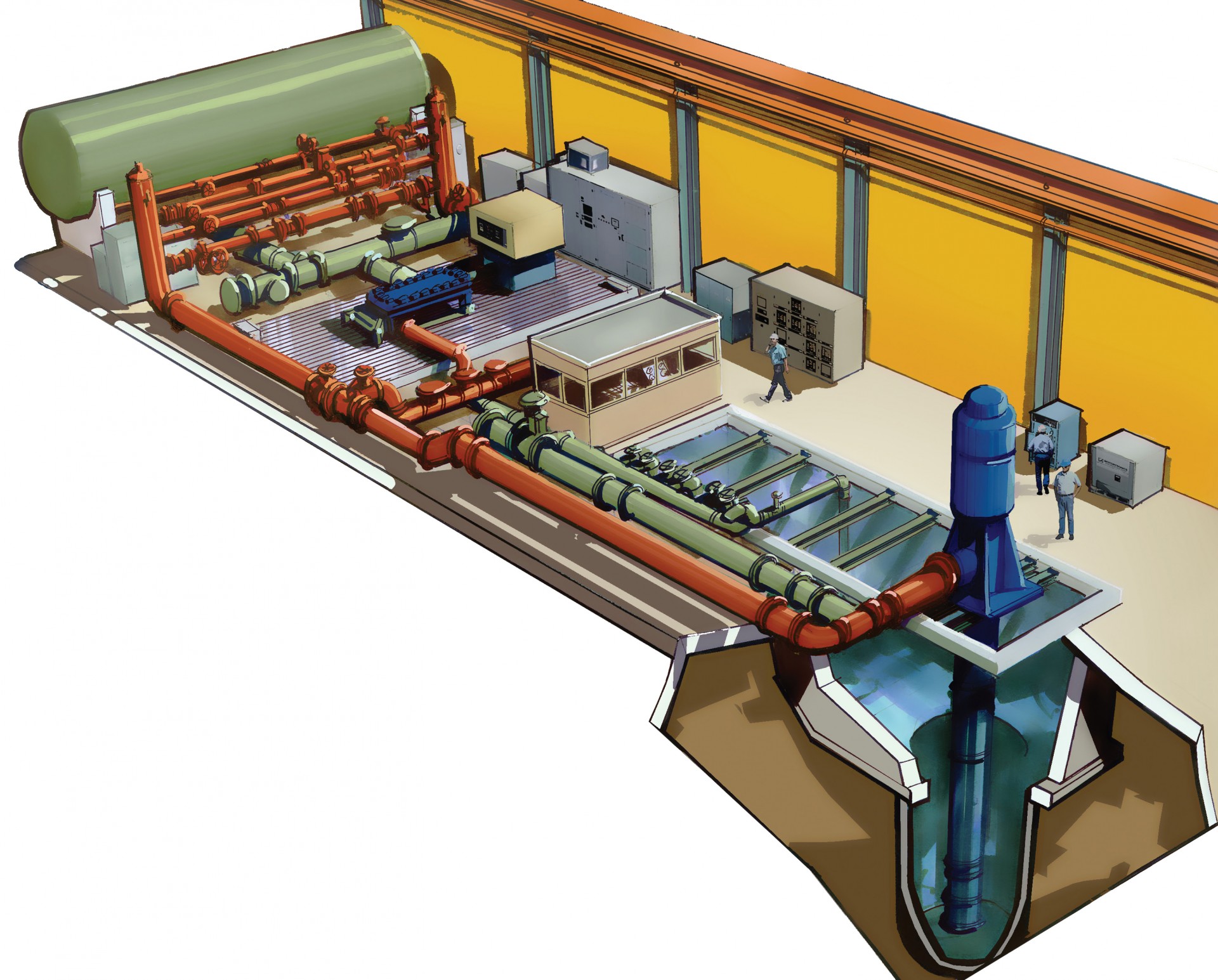
Setting New Standards
The Hydraulic Institute (HI) is a non-profit organization established to enhance the effective, efficient and economic use of pumps through the development of industry pump standards and educational tools for effective application, testing, installation, operation, maintenance, and performance optimization of pumps and pumping systems.
For more information on the Hydraulic Institute's Test Lab Approval Program (PTLAP), visit their website at pumps.org.
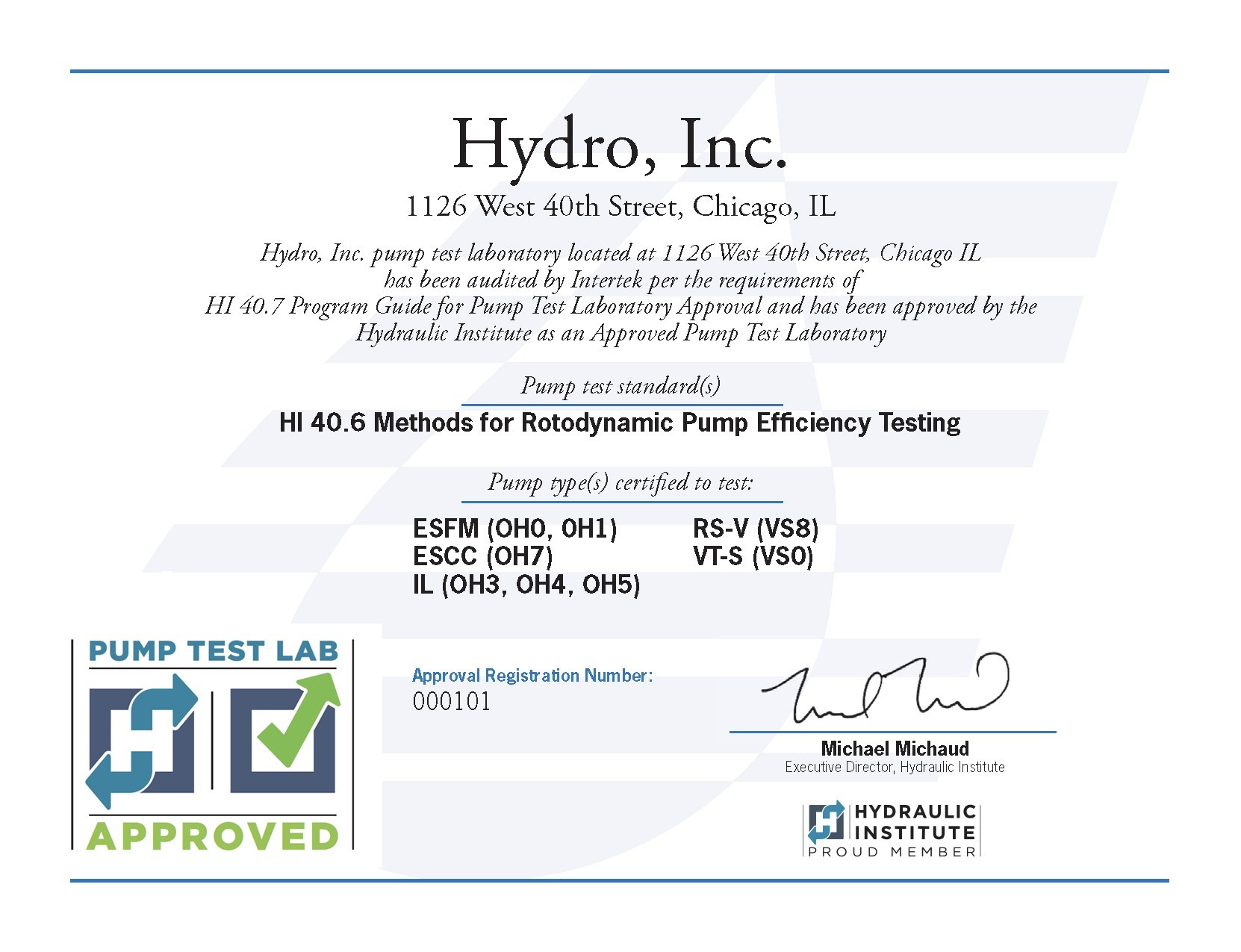
Remote Witness Testing
The Hydro Performance Test Lab is fully equipped to support remote witness testing.
For customers to feel assured of the quality of work being performed as promised, witness testing allows for a transparent and convenient opportunity.
Hydro offers customers the opportunity to witness any part of the job scope–not only performance tests, but setup and installation processes as well. This includes soft foot and pipe strain checks and machine train alignments.
Key Features:
- Meeting sessions through multiple platforms (Teams, Zoom, TurboMeeting, etc.)
- Screen sharing capabilities to show real-time hydraulic and vibration data
- Live video feed of the pump test arrangement from six (6) different camera angles
- Communication with the Test Engineer and other Hydro representatives
- Customers can include multiple team members in the remote witness test meeting sessions (managers, engineers, operators, etc.)
Frequently Asked Questions
You can find answers to some commonly asked questions here in our FAQ section, and if you have more questions, or just want to learn more about how it all works, give us a call. In our world, there is nothing more important than the health of your pumps. We’re partners - not suppliers. We look forward to speaking with you.
The test can be applied to a new pump, refurbished pump, or re-engineered pump with the focus being on reliability, assurance of meeting the required operating conditions, and measuring the actual changes in performance if a change was made.
For example, in an energy optimization project, a pump may be designed to achieve a higher efficiency to save on the operating cost of the unit. A performance test can be completed to validate the engineering and design. If a test is not completed, the end user may be going into operation with only the design engineering and reputation of the vendor to count on.
If a critical speed was present below the maximum pump speed, the pump would be subject to damaging resonant vibrations as it passes through or operates within 10% of the critical speed. By identifying the critical speed in a controlled test environment, the customer can avoid operating the pump at or near the critical speed thereby ensuring safe pumping conditions.
Hydro has a custom-built pump test program based on the flexible platform provided by LabVIEW. It is a state-of-the-art test program.
Similarly, vertical and submersible pumps are installed and connected to existing piping configurations in order minimize setup time and ensure an accurate test.
The largest vertical/submersible pump we can test is 35 ft in length, 60” in diameter, and with flow characteristics that can be simulated in our flow loop – considering adjustments using affinity laws as needed.
Connect with an Expert
Ares Panagoulias | Director of Condition Monitoring and Test Lab
Ares is responsible for engineering, sales, marketing for Condition Monitoring and Test Lab services and products primarily to support the Nuclear (safety and non-safety related), Power Utility, Pipeline, and Oil & Gas industries.
Connect on LinkedIn