A nuclear utility had a large circulating water pump with severe vibration issues that required refurbishment in an emergency time frame. Hydro’s Aston, PA service center, which has a 50-ton crane and a history of providing quality repair for nuclear non-safety related equipment, was chosen for this work. Despite the unique challenges in machining and maneuverability presented by large pumps, the DCI and refurbishment were performed in under 2 weeks. Continue reading
Tag Archives: reverse engineering
Fully Equipped & On the Move
Hydro was called on to reverse engineer a large circulating water pump in the Caribbean to supply parts for refurbishment. The lead times for receiving parts from the original equipment manufacturer (OEM) were excessive. More concerning, the suction bell provided by the OEM had failed during service. All internal ribs were lost, and the bearing holder was found loose within the assembly. Continue reading
Optimum Flow – Expert Solutions When It’s Critical
A major county in California found itself in a crisis when its irrigation pumps could not produce the required performance, cutting off critical water supply to the reservoirs and aqueducts. These pumps suffered from high vibration and repeated failures characterized by extreme wear to the propellers, shafts, and bearings.
State of the Art Parts: Expedited Impeller
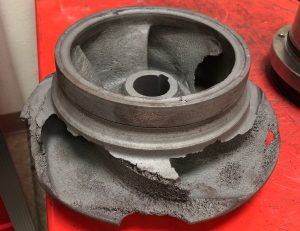
The destroyed sample used for reverse engineering
State of the Art Parts: A Gulf Coast refinery had the primary pump for a critical system at the HydroTex Golden Triangle facility for refurbishment. While the primary pump was in the shop, the backup pump operating on-site began to show signs of failure. The impeller of the pump being repaired had extreme wear and was unable to be reused. The shop needed to source an impeller in an expedited timeframe to complete the repair ahead of schedule and get the primary pump back in service before the backup pump failed. Continue reading
Pitfalls in Puerto Rico: Rescued by Reverse Engineering
When the experts at Hydro were called on to reverse-engineer parts for a large circulating water pump in the Caribbean, they were concerned to discover an OEM-provided suction bell had failed during service. All internal ribs were lost and the bearing holder was found loose within the assembly. Not only had the suction bell failed, but the customer was facing excessive lead times for the parts needed for the refurbishment of the pump.
After a meticulous review of the suction bell design, it became clear that low manufacturing costs had been prioritized over reliability. Instead of providing the customer with a cast component, the OEM had provided a suction bell that had been fabricated, resulting in an excessively thin wall thickness. Continue reading