The Critical Parts Landscape is Changing.
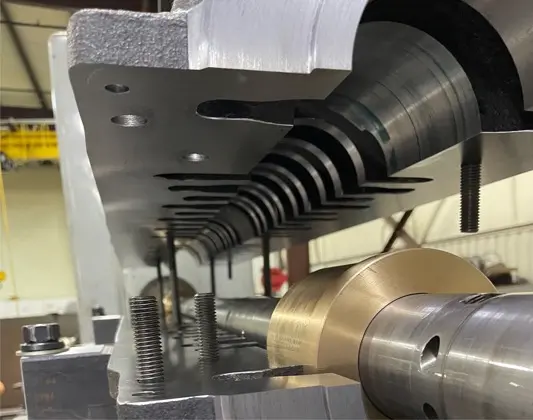
With the advent of innovative pattern making and additive manufacturing, end users have more options than ever before when it comes to parts supply. When faced with these exciting changes, it is important to develop a parts strategy that takes advantage of new technology while still reducing risk of component failure or unsuitability.
At Hydro Parts Solutions, we combine innovation with hard-earned experience in pump engineering, reverse engineering, materials, and casting. Knowing that reverse engineering is far more complex than laser scanning and replication, they rely heavily on this experience and the knowledge of Hydro’s engineering network to verify critical dimensions, account for wear of the scanned component, upgrade tolerances, and provide a part that is better than the original.
By cultivating strong relationships with local foundries, Hydro Parts Solutions can provide expedited lead times while maintaining control of product quality throughout the manufacturing process. They adhere to strict process control procedures, including providing standardized parts numbers and generating drawings for every part.
Every job completed by Hydro Parts Solutions is passed through multiple levels of engineering and inspection checks, from model development through pattern creation to final machining and equivalency analysis. This gives you confidence that the parts supplied will provide safe and reliable service.
As pump experts, Hydro has the experience to reverse engineer and supply complex hydraulic components and the resources to diagnose design problems and suggest targeted upgrades. Hydro routinely upgrades vintage equipment with proven design component design upgrades that counteract known failure modes. Our global engineering team works closely with our parts division to perform hydraulic modifications that increase efficiency or help end users meet changed system requirements.
The end result? Shorter lead times and longer component life.
Explore Hydro Parts Solutions’ state-of-the-art parts case studies.
Discover Hydro Parts Solutions here.
Contact us for a parts quote.