Boost Energy Efficiency and Accelerate Savings
It’s estimated that 85% of pumps are not optimized to their systems, costing end users both efficiency and reliability. To achieve operational excellence and reduce environmental impact, assessing and improving our systems is essential.
There is a lot of focus on buying new equipment with a higher energy efficiency rating. In reality, the efficiency gains available in optimizing efficiency within the pump design is usually dwarfed by the energy savings available by optimizing the way the pump operates within its system. Not only does optimizing a pump to its system result in a reduction in energy usage, it allows the pump to operate at its best efficiency point (BEP), where reliability is the greatest.
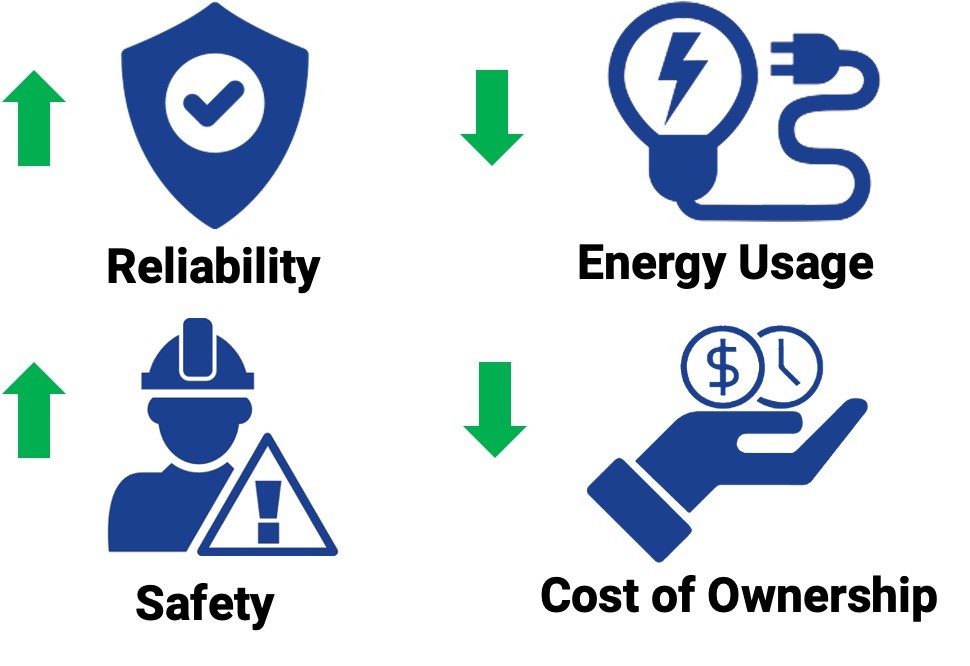
With today’s technology, optimizing a pumping system is achievable with less cost and a greater return on investment. Advancements in testing capabilities and analytical modeling help us to better understand and predict how fluid moves through a system, allowing us to identify more opportunities for improvement. These technologies also eliminate the uncertainty of planned modifications by assessing their effectiveness in a virtual environment.
When optimizing a pump to its system, it’s important to have a holistic mindset- looking beyond the pump boundaries, considering both mechanical and hydraulic performance, and understanding that system operation is affected as much by the people who operate it as it is the physical system itself. What tools are useful to have in your toolbox when approaching a system optimization project?
Continue reading →