As part of Hydro’s support of a Midwest steel mill’s descaling pumps, the Centaur condition monitoring service has been installed on five of their pumps machine trains. Using wireless sensors, Hydro has been continuously collecting real-time vibration and surface temperature levels on the pump, gearbox, and motor. The goal of this monitoring service is to work directly with the end-user to improve rotating equipment maintenance strategies through better, more frequent data collection and Hydro’s subject matter expertise in rotating equipment.
Tag Archives: predictive maintenance
What Happens When Things Go Bump in the Night?
What happens when an alarm is signaled from our Condition Monitoring System? Is the software customizable to customers’ needs? Glad you asked.
It all starts in the home of our Centaur engineers – the Monitoring and Diagnostic Center, where dedicated personnel are checking the status of monitored equipment 24/7. These vibration and pump subject matter experts keep an eye on concerning trends and use the digital twin interface to identify areas of concern. Continue reading
Full Refurbishment for Island Refinery
The process of reopening the plant had uncovered more than 500 pumps that needed considerable refurbishment and repair. The most important of these was a critical jet pump used for hydraulic decoking. It was badly damaged and sent to the original equipment manufacturer (OEM) for inspection. The OEM recommended that the refinery replace most of the pump parts, as well as a costly repair that would require 35 weeks to rebuild.
Viable alternative
Instead, the refinery sent the pump to global aftermarket pump service provider, Hydro, Inc. in Chicago, where it was refurbished for just over half the cost of the OEM proposal. The time involved was also significantly improved to just eight weeks by using a non-destructive evaluation and rebuild process at a 46,000 ft2 facility where Hydro develops and implements engineering modifications for improving the performance of critical pumps and then verifies that performance in their Hydraulic Institute certified test lab.
Significant reopening
The original refinery opened in the mid-1960s. In the early 1970s, it was re-rated at 650,000 barrels per day. It had been one of the largest refineries in the western hemisphere, so the impact of reopening the plant would be significant. In this case, Hydro was tasked to work with the critical highenergy pump to prepare for its reopening. The new owners began the process two years ago and it is expected that the plant will be open for operation in the first quarter of 2020. Once restarted, the plant will be able to process up to 210,000 barrels per day of oil, a fraction of the 1,500- acre (607-hectare) plant’s peak capacity in the 1970s of 650,000 bpd.
When the plant was shut down, the pumps and other equipment in the refinery were either left in place or went into storage where they were kept in poor condition. Time constraints prohibited proper preventative maintenance before the refinery shut down. The tropical climate is hot, salty, humid, oppressive, and several hurricanes occurred during this time. All of these extreme conditions can contribute to the deterioration of heavy rotating equipment. Over the course of the year, the temperature typically varies from 72°F to 88°F and is rarely below 68°F or above 90°F. Continue reading
Engineering Analysis Resolves Startup Issues at Middle Eastern Plant
During the commissioning and startup of an alumina processing plant in the Middle East, a significant recurring pump issue was causing delays to the commissioning of the facility. When de-energizing the equipment, the live steam condensate vertical can pumps experienced repeated failures of all installed units. These seizures occurred at both the design fluid temperature and when pumping cold water.
Because this was a new plant in the commissioning phase, the equipment was under warranty. However, negotiations with the OEM were lengthening the challenged startup schedule. There was little insight into the root cause of the equipment failure.
As the repeated failures were affecting the plant commissioning date, the large architect, engineering and construction (AEC) firm in charge of plant commissioning decided to contact an independent, aftermarket service provider located in Dubai, United Arab Emirates, to conduct an assessment to determine the root cause of the pump failures and provide solutions.
Source: https://www.pumpsandsystems.com/engineering-analysis-resolves-startup-issues-middle-eastern-plant
Wireless Condition Monitoring Optimizes MTBR
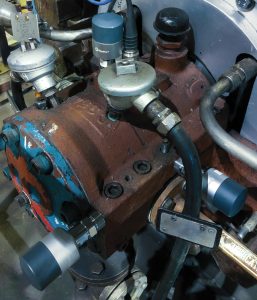
Working in partnership with the plant condition monitoring team, the PIEs installed a total of nine SDOF (Single Degree of Freedom) wireless vibration sensors on the pump and drive.
Alerts, advanced analysis, and automated reporting help to improve maintenance strategies and critical asset decision-making.
A power plant in Southeast Australia had recently experienced chronic high vibration amplitudes on a critical multistage boiler feed water pump. Given the criticality of the pump and the risks associated with catastrophic pump failure, the power plant contacted Hydro Australia for support.
In collaboration with Hydro, Inc.’s wireless condition monitoring team, Hydro Australia was able to provide the power plant with a significantly improved IIoT-based monitoring system. This would assist the plant by closely monitoring the status of its asset, making the best possible decisions for equipment maintenance, and ensuring equipment availability
Source: https://www.pumpindustry.com.au/wireless-condition-monitoring-optimises-mean-time-between-repair