As part of Hydro’s support of a Midwest steel mill’s descaling pumps, the Centaur condition monitoring service has been installed on five of their pumps machine trains. Using wireless sensors, Hydro has been continuously collecting real-time vibration and surface temperature levels on the pump, gearbox, and motor. The goal of this monitoring service is to work directly with the end-user to improve rotating equipment maintenance strategies through better, more frequent data collection and Hydro’s subject matter expertise in rotating equipment.
The value of having continuous monitoring was proven during a vibration even that occurred shortly after the installation of a newly refurbished rotor on one of the pumps. After noticing a concerning upward trend in vibration, Centaur’s engineering team suspected that the pump was suffering from structural looseness in the outboard bearing housing. Learn more about how the discovery and remediation of this vibration transpired in the timeline below.
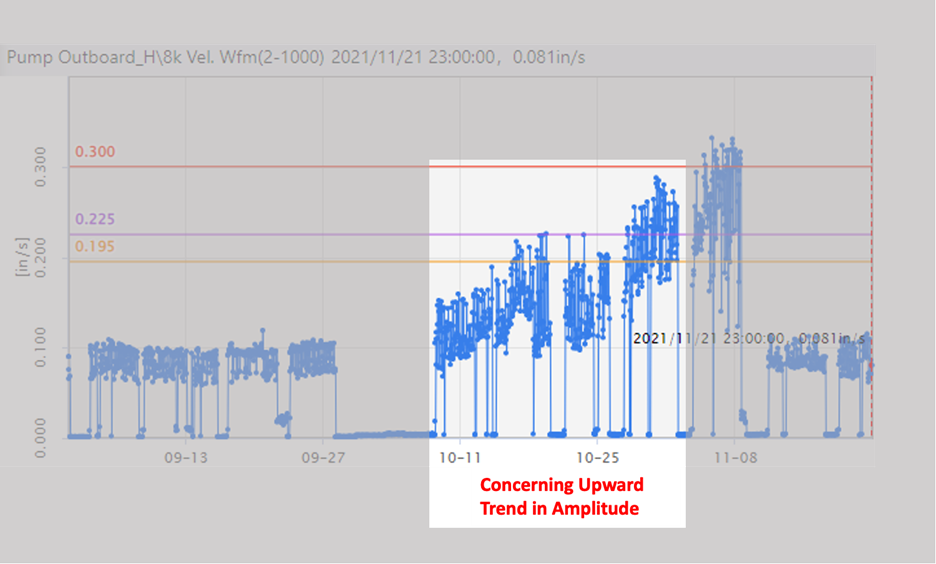
