
Figure 1. The pump as received
Many pumps in operation today were designed and manufactured decades ago. As plants require increased capacity, pump systems are expected to meet these higher process flow demands. Without an impeller rerate or change in speed, this increased capacity can be achieved in one of two ways. The individual pumps can supply more flow to the system, resulting in operation out on the pump curve. Alternatively, capacity can be increased by operating more pumps in parallel; in this case operation is pushed back on the curve, as operating another pump in parallel requires less flow from each individual pump to meet total system demand.
Either operational change results in a move away from the pump best efficiency point (BEP). As a result, the original designs and hydraulic characteristics no longer effectively meet plant requirements and detrimental effects from hydraulic instability can occur.
By way of example, this article will discuss a fertilizer plant in the Gulf of Mexico that had a boiler feedwater pump unit that was experiencing performance problems after a significant plant expansion project. Unfortunately, it was not the first time this particular unit had experienced a loss of capacity; the pump had been in operation only 18 months prior to the current issue.
In some cases, a successful pump repair can be as simple as performing a comprehensive inspection, reinstating fits and rotor position, checking for pipe strain, and conducting laser alignment between the motor and pump when the pump is installed. However, the recurrence of a problem indicates that a design issue may be present.
The plant uprate, resulting in changed operating conditions, could have caused undesirable effects due to non-optimal operation. Rerates are often required to meet new operating conditions and achieve desired reliability and efficiency. In cases where a rerate is not feasible due to time or financial constraints, upgrades are necessary to mitigate the effects of damaging hydraulic behavior.
To ensure that the correct course of action was identified, the plant recognized the importance of choosing a pump service provider that had the experience and engineering capability to effectively diagnose and resolve the root causes of the performance degradation. When the original manufacturer responded with a long repair lead-time, the plant chose to seek an alternative solution to correct the performance issues.
In this case, the client’s sister plant recommended an aftermarket pump service provider that had the technical and engineering expertise to not only repair and rebuild the pump to the highest quality standards but also forensically diagnose and resolve all underlying issues. Working together, the site and service provider were able to determine the causes of degradation and devise a comprehensive plan to resolve the issues, ensuring safe, reliable operation of the equipment.
Preliminary investigation
A loss of pump capacity can usually be attributed to damaged or worn hydraulic components, cavitation, or internal recirculation. In the case of internal recirculation, not all of the flow that is produced by the hydraulic element makes it out into the system. The suction flow is different to the discharge flow by the amount of the internal flow circulation. Pumps that operate in a system with a flow control valve have the ability to decrease system resistance by increasing the valve opening, allowing the pump to operate farther out on the curve and achieve required system flow as internal recirculation increases. However, as performance continues to degrade, a point will be reached where the valve is fully open and no more flow can be recovered. Problems related to operation out on the curve, such as high vibration and a greater likelihood of cavitation, can also occur as the pump flow requirement increases to make up for the recirculated fluid.
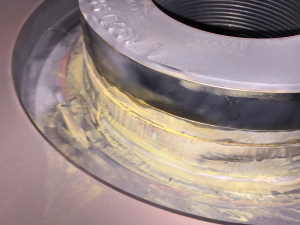
Figure 2. Damaged centring ring seat in discharge cover.
As the boiler feedwater pump performance trended towards unacceptable levels, the site recognised that it was necessary to take the pump out of service. To help establish a resolution, a representative from the aftermarket pump service provider met with the plant’s rotating equipment engineer to review the historic operating conditions of the unit, troubleshoot the design, and discuss possible solutions to rectify its performance problems.
Both parties recognised that a high level of diligence was required to identify the failure mode and ensure that the appropriate corrective action was deployed. During this discussion, the service provider explained that for high-energy pumping equipment, such as boiler feedwater units, the precision of a rebuild is essential, and shortcuts in this process can have significant reliability consequences.
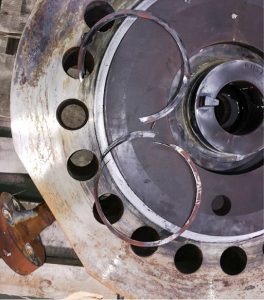
Figure 3. Discharge cover on assembly showing the cracked shims.
With this new information, the plant manager decided to proceed with the proposed forensic inspection plan. The service provider opted to have the pump sent to a service centre in Houston, Texas, US, for in-depth analysis and repair. The client agreed, and the entire unit, including the casing, was shipped for service (Figure 1).
Inspection and forensics
A thorough and detailed inspection process can set the foundation of a quality repair in preventing recurring problems, extending pump life, and reducing long-term repair costs. During the inspection process, issues are often uncovered which, if left unattended, can result in premature failure of a component or the pump itself. In executing a comprehensive inspection process, engineers and technicians can work with end-users to discuss options for not only repairing but for improving the pump’s performance and reliability.
During the inspection a comprehensive forensic analysis was performed on the unit. As the unit was disassembled, any indications of contact, wear, or other abnormal conditions were recorded and photographed as evidence to be used during later analysis. A significant number of dimensions were recorded to capture as-found radial and axial relationships between the components.
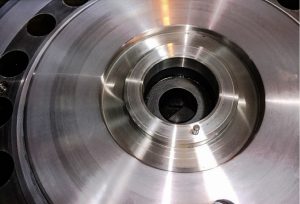
Figure 4. Discharge cover after final machining.
The in-depth inspection process uncovered a range of serious issues, including a damaged centring ring seat in the discharge cover (Figure 2). Most significantly, severe erosion of the suction pressure face was observed. It was determined that this erosion was due to insufficient gasket compression. The original design contained a shim compensation pack containing multiple shims (Figure 3). This shim pack was not sized correctly, leading to the failure of the internal suction head gasket.
Analysis
The dimensional analysis of the pump components revealed that the shim compensation pack was not thick enough to provide sufficient compression on the internal suction head gasket. The suction head gasket seals the face between the suction entry, at suction pressure, and the chamber surrounding the internal volute element, at discharge pressure. This high differential pressure makes it crucial to provide a sealing arrangement that prevents internal recirculation. Flow is driven from high pressure to low pressure areas and costly erosion damage occurs to the barrel.
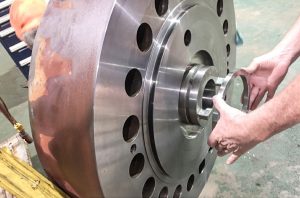
Figure 5. The volute locating ring being installed.
The combination of the discharge head extension that protrudes into the casing, the shim compensator set, and the internal assembly determines the crush on the internal suction gasket. The insufficient thickness of the compensator shims resulted in an unloaded gasket, preventing the formation of an effective seal. The failure of this gasket allowed internal leakage from the high pressure discharge chamber back to suction.
High energy designs are especially susceptible to leakage due to design or assembly errors such as this because of the high pressure differential between suction and discharge. Precision is required across many components as a combination of manufacturing tolerances across multiple pieces can lead to an overall dimensional error, even if each individual component is considered acceptable. Tolerance stack and geomantic tolerances can become a serious problem. Damage to a gasket, insufficient loading, or uneven loading can quickly lead to extensive erosive wear of the barrel and internal element as high local fluid velocities, driven by the high differential pressure across these small leak paths, erode the components.
Another factor that may have contributed to the performance degradation was the operation of the pump away from the BEP. At the BEP, the angle of the fluid velocity matches the stationary blade geometry of the impeller and diffuser, resulting in minimal losses. As operation deviates from the BEP, the fluid and stationary blade angles deviate as well, resulting in a susceptibility to fluid recirculation at both the suction and discharge of the impeller.
Off-BEP operation results in higher radial loads, increased vibration, greater probability of instability-induced cavitation, and other highly detrimental effects. As vibration increases, the likelihood of component contact and wear also increases. Contact and wear usually occurs in the close clearance wear ring interface – a clearance that is crucial to maintain for reliable operation. In addition to limiting internal recirculation, the wear ring acts as a fluid-lubricated bearing, providing stiffness and damping to the rotor.
Complex multi-stage designs have a multitude of nested radial fits that must be closely maintained to ensure centreline compatibility of the rotor to the stator. In this particular case, the combined effect of the tolerances of the assembly was not stringent enough to deter contact. As the stiffness and damping provided by the wear rings decreased, there was a reduced ability to ameliorate the negative effects of operation away from the BEP. The poor axial position of the impellers within their volutes also aggravated the effects of hydraulic instability. When a design is not mechanically robust, the effects of a non-optimal hydraulic design or a system upset are more likely to cause damage and that damage is more likely to be costly or catastrophic.
Solution
In engineering a long-term solution, the service provider outlined and executed a scope of work, including repair, assembly, and pump installation. The first step to providing a more robust machine was to ensure that all critical fits were reinstated to best-in-class standards, including component fit-ups, concentricity of critical bores and locating diameters, and perpendicularity of critical faces. The dimensional analysis performed during inspection was used to make small adjustments that ensured that each impeller was axially centred within its respective volute. Verification of the bearing housing alignment and re-doweling were also performed to ensure radial centralisation of the rotor within the stator.
To resolve the internal recirculation caused by insufficient gasket crush, the comprehensive work scope also included a rebuild of the volute assembly with an upgraded steel jacketed gasket and a redesign that removed the compensator shim set. This design included a volute locating ring and a full upgrade to the discharge cover and barrel casing to ensure proper gasket crush was achieved. The discharge cover was installed with a corrected location, and gasket loads were ensured by the precision locating ring (Figure 4).
The solution, whilst appearing to be relatively straightforward, required significant engineering knowledge of high-energy pumping equipment. Utilising a correctly sized precision locating ring addressed the pump reliability issues (Figure 5). After installing the ring and ensuring the precision of the component locations and the build quality, the pump ran at its desired operating point.
Conclusion
While manufacturers traditionally focus on repairing their own equipment, an independent aftermarket service provider can draw upon an expanded knowledge base that includes experience across a broad spectrum of pump manufacturers and pump designs. This, in turn, can provide insights on the success or failure of different hydraulic designs, material upgrades, and mechanical improvements in specific applications and operating environments.
After the job was completed, the plant rotating equipment engineer went onsite to ensure that the unit was performing as expected. The service provider was consequently informed that they would become the preferred vendor for future servicing.
This case shows that technical capability, in addition to a careful and detailed rebuild process, is of crucial importance when servicing high pressure, multistage boiler feedwater pumps. Very rarely does a pump operate in the conditions for which it was originally designed and tested. Changing system requirements, ageing installations, deficient tolerances, and improper assembly practices can all contribute to equipment degradation and failure. Being able to provide a forensic analysis and having the technical knowledge to understand and predict mechanically and hydraulically induced influences, such as operation away from the BEP, is crucial to being able to analyse and resolve problems. Engineering is at the heart of a quality repair.
Authored by Dave Allard.
Source: worldfertilizer.com