A large Midwestern coal-fired power plant had been experiencing vibration issues and premature failures with their large Kirloskar 130 BHM circulating water pumps. The plant has two operating units, with three circulating water pumps installed in each unit. The average life of the equipment was 6 months, which is far belong the industry standard for a large vertical turbine pump in this service. The pumps were sent to Hydro’s HydroAire 40th Street service center for a causal analysis and remediation of any problems that were found during the investigation.
Upon disassembly, it became apparent that there were several critical issues that needed to be addressed to increase the reliability and mean-time-between-repairs for this equipment. The discharge head gussets were heavily eroded clear cracks and dislocation, which weakened the discharge head assembly and made is susceptible to high vibration.
The stuffing box was also eroded, which would make it difficult to successfully perform pump-to-motor alignment in the field upon reassembly at the site.
Another area that added to the high vibration was excessive bearing clearances. The guide bearings and shaft sleeves exhibited excessive wear, which would have reduced the stiffness and damping of the rotor assembly. Several factors were likely contributors to the bearing wear.
Fit-ups of the stationary assembly were excessive with average fit-ups measuring in the range of 0.010 – 0.030”; for reference, Hydro’s typical acceptance criteria are 0.001 – 0.003”. Critical faces and bores were also found out of acceptable tolerance, with concentricity, parallelism, and perpendicularity measuring in the range of 0.005 – 0.015”, where acceptance is usually held less than 0.002”. Not only did the out of tolerance fits contribute to overall misalignment, they provided a leak path that resulted in erosion of the column pipes at the fit areas.
Excessive wear was also found on the impeller vanes and the impeller liner surface, indicating contact between these two components. This contact was likely caused by both the overly loose impeller fit and non-concentricity of the rotor and stator, as mentioned above. The impeller vane wear would have increased rotor imbalance, further increasing vibration. The opening of this clearance would have also reduced the pump efficiency, causing it to lose performance and require more energy to operate.
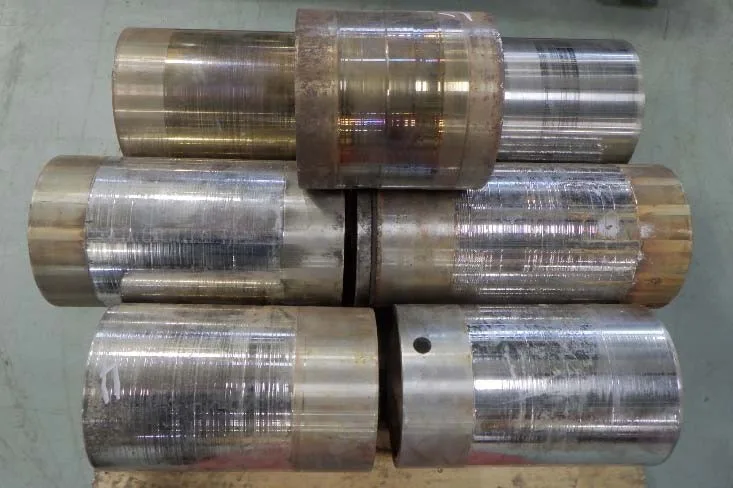
In addition to the factors that likely caused misalignment and contact between the stator and rotor was that the fluid being pumped had a high sand content, which made it an especially harsh environment for the bearings and sleeves. The shaft sleeves were found to be a hardness of only 32Rc, which was insufficiently hard to resist wear. The shafts themselves also exhibited wear at the sleeve location, which increased the overall cost of maintenance for this equipment. The guide bearings were self-lubricating soft bearings made from a composite material and did not have any fluting to allow particulate in the fluid to pass more easily through the tight clearance without wear and were deemed inappropriate for this application.
Modifications were designed to provide structural reinforcement to the discharge head and to eliminate the factors causing premature wear of the bearings and shaft sleeves. The eroded gussets were removed and replaced with thicker, more robust gusset to enhance the structural integrity of the components. The new gussets and lifting lugs were fabricated from carbon steel and installed using precision welding. A PT inspection was completed to ensure weld integrity. The eroded stuffing box was also repaired using weld restoration techniques.
To improve the alignment of all components within the stationary assembly, any out of tolerance fits and bores were welded up and machined to best-in-class tolerances and fits.
Vertical pumps are especially susceptible to misalignment since they have a large number of stacked components. Large fit-ups between each component can easily stack-up to a large offset at the bottom of the assembly that exceeds the bearing clearance. By restoring recommended fits and tolerances, non-centerline compatibility between the stationary and rotating elements would be greatly decreased.
The impeller was laser scanned to create a solid model of the component that could be used to establish the correct vane profile of the component before it had been worn. This model was used to create the vane profile machining drawing that was used during impeller refurbishment. The solid model was also used post-machining to confirm that the machined component conformed to the expected dimensions during as-built inspection. The impeller bore was also corrected to provide the appropriate fit-up to the shaft.
To add additional wear resistance, the shaft sleeves were upgraded to 410 stainless steel and provided with direct laser deposition (DLD) cladding on the running surface to enhance durability and wear resistance. The shafts were chrome plated at the fit locations to extend their service life as well. The bearings were upgraded to a cutlass rubber design that included axial grooving to improve longevity and overall pump performance.
The impact of these enhancements was clear upon reinstallation of the pump at the power plant. The modifications significantly improved the pump’s structural integrity, alignment precision, and wear resistance. By implementing these targeted upgrades and providing a quality repair, Hydro was able to ensure that the end user would achieve reliable performance in demanding operating conditions. The reinstalled pumps have now been operating for more than 3 years, which is already 6 times the life they had previously been experiencing. The high vibration was eliminated and vibration is now measuring below any alert or alarm levels.
Interested in learning more about our HydroAire 40th Street facility? Meet them here.
You can also explore our experience with large vertical pumps here.