Hydro’s Condition Monitoring system, Centaur, has aided many end-users in catching real-time faults in rotating machinery. In many instances, end users see the value of the system through a no-cost, on-site trial. This includes the hardware, installation support, commissioning, and monitoring starting from the date that the sensors are commissioned on-site. The purpose of the free trial is to allow a “proof-of-concept” evaluation period before a further commitment is made. Continue reading
Tag Archives: wireless condition monitoring
Wireless Sensor Data Integration Into Existing Plant Historian
A large American energy company wanted a new data collection system to be integrated into its site historian along with process trending software to better diagnose system-related issues that can lead to maintenance issues.
Thanks to the help of an aftermarket service company, the energy company combined multiple sources of data and can now view complex mechanical vibration phenomena in parallel with plant process data. By comparing the two sets of data side by side, plant personnel will correlate process conditions with mechanical vibration data.
The service provider’s history of pump and rotating equipment knowledge helped to provide actionable analysis of pumps and other rotating equipment health—and a mechanism to provide additional engineering solutions to complex problems. Combined with the energy company’s focus on reliability and a history of maintaining their equipment, this system provided an improved method of data collection and analysis.
Source: https://www.pumpsandsystems.com/wireless-sensor-data-integration-existing-plant-historian
Meet Centaur, Hydro’s Wireless Condition Monitoring Solution
Hydro, Inc. introduces Centaur, its Wireless Condition Monitoring Solution. Centaur provides users with remote monitoring allowing for operators and engineers to observe equipment performance in real-time enabling predictive analytics, vibration monitoring, and temperature readings to optimize critical asset maintenance strategies.
Centaur offers advanced data analysis support, backed by Hydro’s diversified and unbiased pump knowledge base, which spans across a broad spectrum of manufacturers and designs. With highly customized dashboards and automated alarm notifications, Centaur can alert users before a critical asset experiences a failure or previously unforeseen event.
The benefits realized with Hydro’s Wireless Condition Monitoring Solution are:
- Real-time data – not dependent on the next route cycle
- High-frequency data collection – no more missed events or issues
- Increased safety resources available for data analysis – reducing in-field data collection time increases availability for analysis
- Customizable alerts and alarms give users the assurance to operate their machines without concern
- Maintenance schedules can be optimized based on machine condition
For over 50 years, Hydro has been providing customers with creative engineering solutions to complex pump problems. Now, Hydro offers 360° support for customers’ rotating machinery with Centaur: Hydro’s Wireless Condition Monitoring Solution.
Do you have concerns regarding your critical asset reliability? Visit https://hydroinc.com/centaur or call 1-800-223-7867 to learn more about Hydro’s suite of services.
Maximizing Efficiency in Descaling Pumps
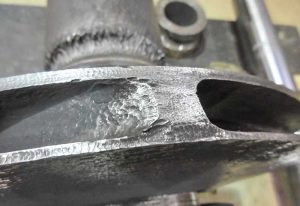
Damaged impeller showcasing severe corrosion.
A major steel plant on the East Coast had been experiencing catastrophic failures with its five-stage descaling pumps. The plant operated using three multistage axially split (BB3) pumps with two spares. All five of the pumps had a mean time between repair (MTBR) of two years. In this case, the plant water quality was considered to be less than ideal, and the entrained abrasives were a factor contributing to the repeated failures.
Poor water quality can lead to a number of pump reliability issues. When pumping fluids with abrasive material, pumps experience erosion and corrosion, and the effects can rapidly degrade both the casings and critical inner elements. While erosion and corrosion alone are not always a difficult problem to solve, it is important to have a firm understanding of the relationship between various types of erosion and corrosion and the metallurgy used in designing the pumps.
Further analysis showcased excessive clearances and inconsistencies with component fits that also contributed to pump performance degradation outside the abrasion. In order to increase the MTBR of the pumps at the plant, the aftermarket pump service provider recommended several engineered upgrades including new impellers to be manufactured using advanced mold technology, specifically addressing the surface finish and dimensional consistency.
Source: https://www.pumpsandsystems.com/maximizing-efficiency-descaling-pumps