Additive manufacturing also improves geometric tolerances.
Written by: Jesse Stinson (Hydro Parts Solutions) & Werner Barnard (Hydro Inc.)
Publisher: Pumps & Systems / March 2, 2015
An increasing number of industrial plants are reducing the spare parts inventories stored at their facilities. At the same time, they are replacing fewer pumps because of capital constraints and have determined that remanufacturing existing equipment is the best path forward. Many of the pumps within these facilities have exceeded 50 years of service. This drives the need for replacement parts and, in some cases, emergency replacement parts. Considering the age of these pumps, the replacement parts from the manufacturer are likely obsolete and may not be easily available. Further complicating the situation is the location of manufacture. Many cast parts are manufactured outside the U.S and have long lead times.
To address these challenges, many companies are developing technologies to meet the specific and growing demands of the industry. Many of these advanced tools, including coordinate measure machine (CMM) technology, allow for quicker emergency repairs, faster deliveries and higher quality pump parts.
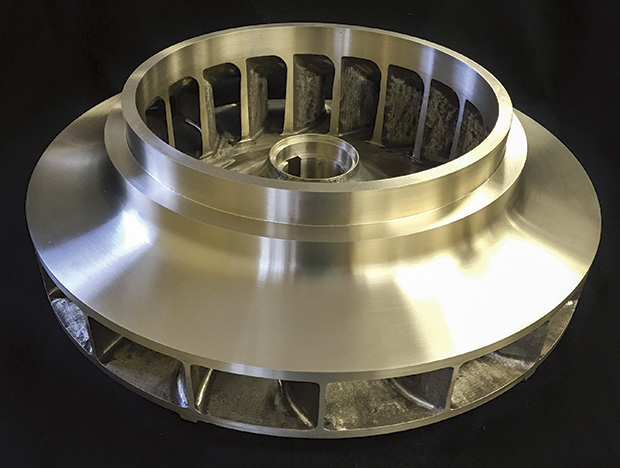
Image 1. New bronze impeller casting (Images and graphics courtesy of Hydro Inc.)

Figure 1. Reverse engineering raw scan data
Emergency equipment repairs are common throughout the industry. Having fewer spare parts makes this classification of repair more challenging. Standard equipment repairs typically take six to eight weeks, while emergency repairs must be completed within one day to three weeks, depending on the severity of the situation.
This type of repair often drives the need for rapidly supplied cast parts, which traditionally require long lead times because of the use of wooden tooling to create the mold to manufacture the casting.
Recent advancements in 3-D technology, known as additive manufacturing, allow the cast parts manufacturer to meet customer demands by eliminating the need to create traditional tooling.