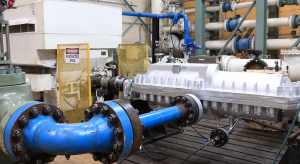
The 14-stage boiler feedwater pump installed for testing to ensure that the performance achieves desired operating conditions.
At a combined cycle power plant, a boiler feedwater pump was experiencing problems. Dr. Gary Dyson of Hydro, Inc. and Larry White of HydroTex discuss how major cost savings were provided through engineering analysis, material upgrades and testing for validation.
A combined cycle power plant in the Pan Handle region of Texas found themselves experiencing repeated failure on one of their 14 stage boiler feedwater (BB3) pumps. The pump had recently been modified by the supplier to provide a short-term solution. This in turn reduced the mean time between failure (MTBF) of the pump, requiring continued support and further analysis.
Combined cycle plants are comprised of both gas and steam power production technologies, capable of producing up to 50% more electricity than traditional simple-cycle plants. With the ever-increasing demand for energy, this technology is becoming increasingly relevant in throughout the pump industry. As such, it is highly important that these plants operate at peak efficiency.
Originally, the stationary inserts at several locations in the pump assembly were modified in such a way that increased the likelihood of friction and galling of the stationary and rotating parts of the pump assembly. The consecutive failures experienced on site were repeatedly of the same failure mode, which strongly points toward a pump design problem.
Authored by Gary Dyson, Ares Panagoulias, Larry White, and Chris Brown.
Source: worldpumps.com