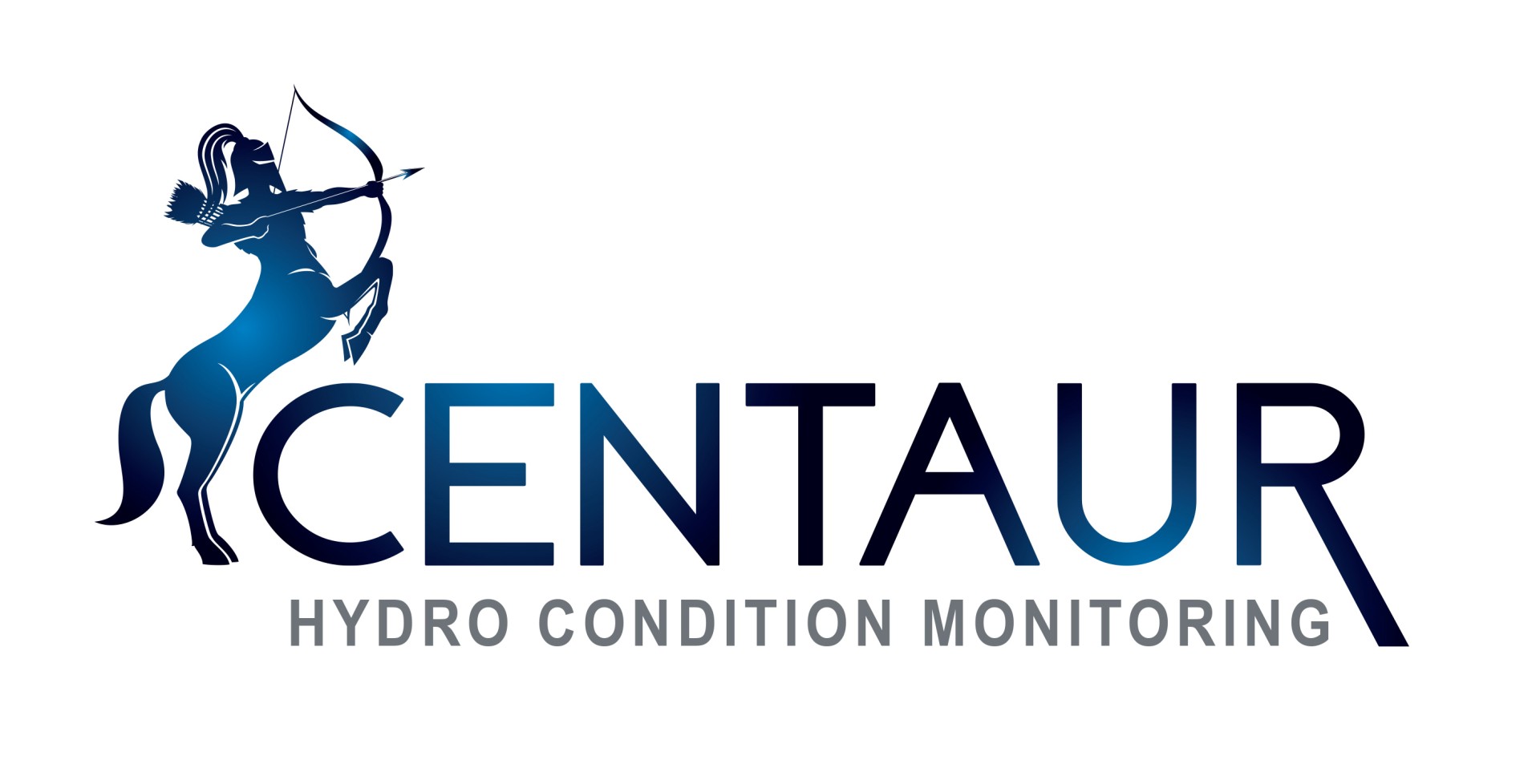
Hydro’s Centaur is an IoT condition monitoring solution developed by rotating equipment experts with a specific focus on detecting equipment failure modes and providing impending warning of incipient problems. Centaur includes the necessary hardware, software, and dedicated engineering support to successfully trend equipment condition and avoid unplanned downtime.
The Problem
Industrial users have relied on analog gauges and route-based data collection methods for decades. These methods often lead to inaccurate or incomplete readings and can expose workers to elevated safety risks, especially in hazardous environments. More importantly, traditional methods do not provide the benefits that continuous monitoring does, such as early detection and warning alerts, remote support for troubleshooting and diagnostics, and improved MTBR/MTBF.
Our Solution
A complete picture of equipment health can only be revealed by capturing a continuous stream of data and using both analytical power and subject matter expertise to turn this data into actionable information. Centaur achieves this by combining digital vibration, temperature, and pressure sensors, cloud-based software, and the experience gained through 50 years of developing aftermarket solutions for rotating equipment.
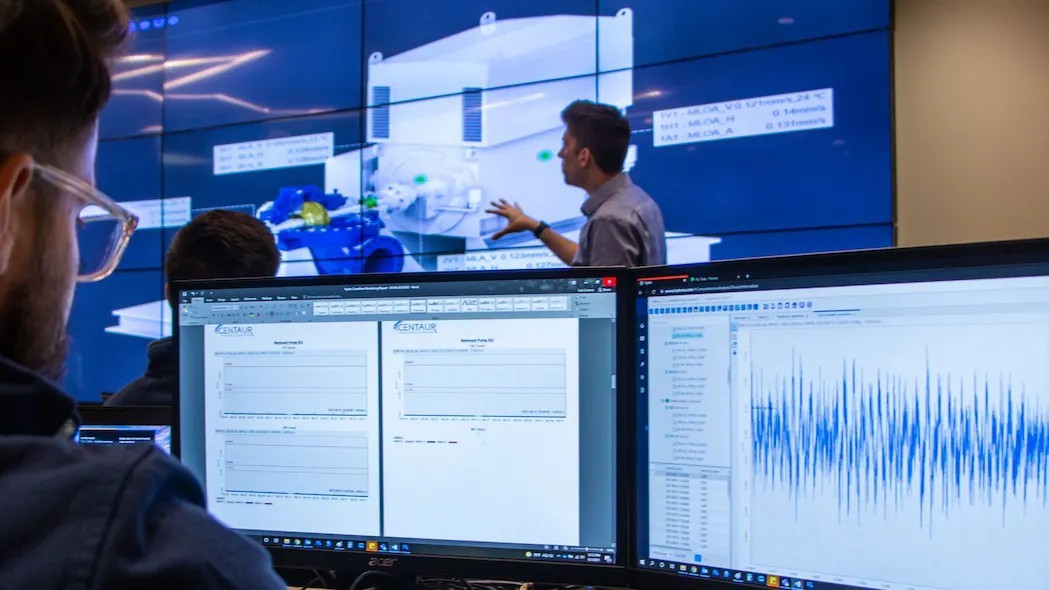
A critical piece of Centaur’s ability to reduce users’ cost of asset ownership and avoid unnecessary downtime is its dedicated engineering team, who provide proactive monitoring oversight, monthly health reports, and advanced analytical support. These rotating equipment experts perform root cause analyses of concerning trends and alarm events, which include recommended action steps to remediate suspected issues long before they become costly failures.
The Difference
In contrast to traditional IOT companies, Centaur was developed with the input of rotating equipment experts. As an unbiased presence in the aftermarket, Hydro has amassed experience over a broad spectrum of manufacturers, designs, and applications.
This expertise influenced hardware and software design, ensuring that Centaur is capable of effectively detecting and identifying known equipment failure modes. Some examples include the measurement of phase data and a frequency range capable of detecting bearing fault frequencies.
How it Works
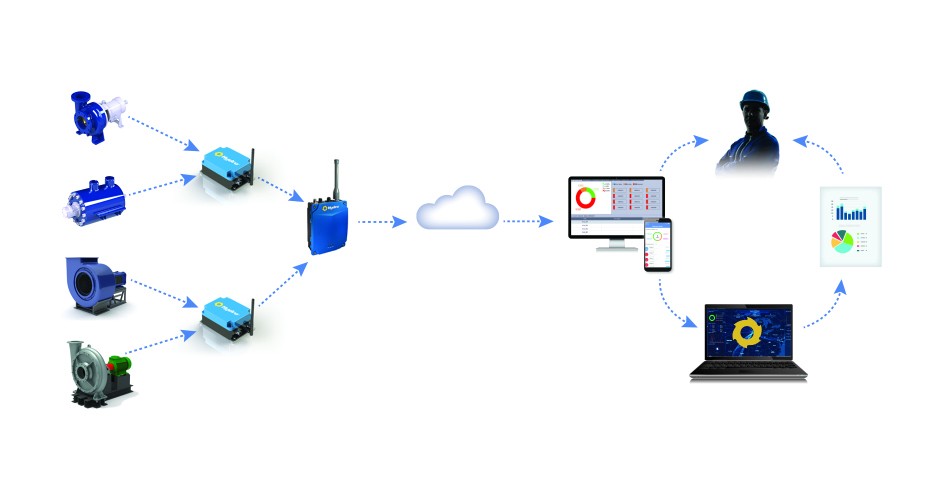
The Benefits
- Increased accuracy: Provides more precise pressure readings, maintaining safe and efficient operations.
- Greater data collection frequency: Allows creation of detailed pressure profiles and trends, supporting identification of anomalies that indicate potential issues.
- Increased worker safety: Eliminates need for workers to access dangerous or hard-to-reach areas and provides earlier warning of potential safety issues.
- Predictive maintenance: Enables condition-based maintenance by tracking performance degradation over time.
- Cost savings: Reduces cost of equipment ownership by preventing potential issues and reducing downtime.
- Trending efficiency: Detecting and trending performance degradation facilitates more informed decisions on equipment operation and maintenance.
Ready to learn more about Centaur? Contact us or apply for a free trial.