A comprehensive approach to reverse engineering helped to establish the differences between the stainless steel and original bronze impellers.
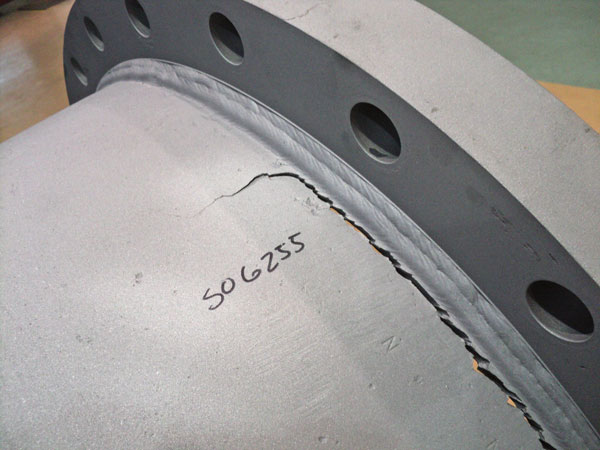
Image 1. A crack in the discharge head flange that involved fatigue failure of the weld of a pump.
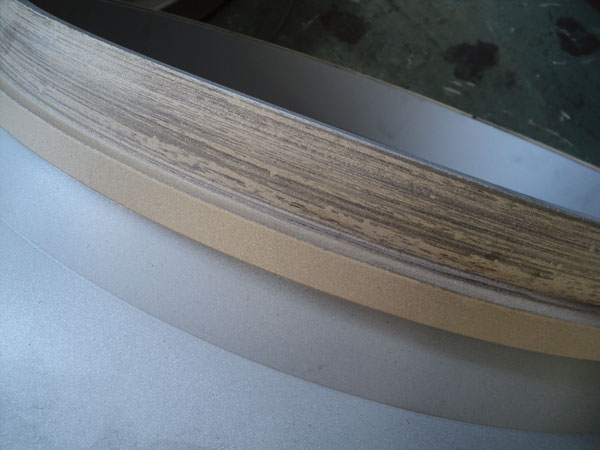
Image 2 (right). The pump’s impeller wear ring landing shows heavy scoring.
The equipment in question consisted of three-stage vertical turbine pumps running either in standalone or in parallel operation as required. The failure manifested itself through high vibration and caused severe scoring of the pump shaft and wear ring landings, leading to fatigue failure of the weld on the discharge head flange (see Images 1 and 2). The commissioned pump was refurbished and rebuilt by another company’s service center with spare impellers supplied by an original equipment manufacturer. No changes to the geometry had reportedly been made, although the impeller material had been upgraded from bronze to stainless steel.
The plant initiated its internal root-cause analysis process, and the failed pump required emergency repair. The station sought a company to conduct the repair, and the firm reviewed the customer-supplied documents and background providing the possible causes of the failure. Continue reading →