-
Reverse Engineering
Reverse engineering is the examination, testing, and analysis of a component to define and document all of the parameters and critical attributes necessary to manufacture, repair or modify it. Dimensions, tolerances, surface finishes, and fit or clearance to adjoining items are determined.
Moving Beyond Replication.
Here at Hydro, we use our expertise in pump design to ensure that every part we manufacture is equal to or better than the original. That’s why we engage our engineering team to review every part we create, both in the reverse engineering stage and during an equivalency analysis after final machining. They ensure that all hydraulic geometry is correct and specify manufacturing tolerances that meet Hydro’s industry-leading standards.
Hydro’s reverse engineering workflow includes a variety of innovation and state-of-the-art technology solutions:
- Hydro has developed our own rigorous process and design control procedures for reverse engineering to provide a competitive and reliable alternative.
- Portable all-in-one coordinate-measuring machine (CMM) for advanced laser scanning of intricate components
- Sophisticated 3D modeling and deviation analysis software capabilities
- Proprietary engineering standards in conjunction with industry standards and design control processes
- Integrated manufacturing process via Hydro Parts Solutions provides component repeatability with a high degree of accuracy and supports emergency parts requirements
Comprehensive Design Analysis
A part provided by Hydro is often better than the original. Design flaws are identified and corrected, tolerances are specified to higher standards, and modeling technology is used to minimize the possibility of casting defects. All reverse engineered components go through a rigorous equivalency analysis (validation that components are identical to that of the original) to identify any divergence between the original scanned component and the manufactured part.
- In addition to being supplied with parts, a power plant is also typically looking for an organization to support them in the event of any future problems issues arising with a piece of equipment.
- All reverse engineering efforts are not the same. Laser scanning and 3D printing of metal parts are not enough to achieve adequate component design. There needs to be a strong engineering approach taking all aspects of the design.
- At Hydro we can ensure the capture of enough information to fully support the plot in dealing with future pump issues.
- Machines are calibrated on a regular basis
- Ability to provide on-site support and portability to complex pump projects
Proven Industry Experience
Hydro understands that reverse engineering is more than just scanning parts–it’s the ability to perform a full engineering analysis to ensure that a part adheres to the original intent of form, fit, and function. Review of the hydraulic, mechanical, and material characteristics of the component is necessary to avoid incorrect final geometry or failure of the part.
- Hydro has a strong history in the industry; we have been reverse engineering for thousands of critical pumps for over 30 years.
- Reverse engineering, laser scanning and 3D metal printing mark the beginning and end of creating new parts
- HydroAire has reliably supplied pump parts for both safety-related and code services to many nuclear plants nationwide.
- Hydro is an end-user focused company with the technical capability and in-depth experience to provide optimal solutions for our customers.
- Creating the final design drawing of a pump component requires engineering guidance and expert decisions
- Our engineering standards define and control how we obtain relevant application information, materials of construction, and part geometry for components we produce, therefore assuring the proper design and material of the components we provide.
Engineering Makes All the Difference
To achieve the best result for our customers, expert engineering is supported by the latest technology and proven process control procedures.
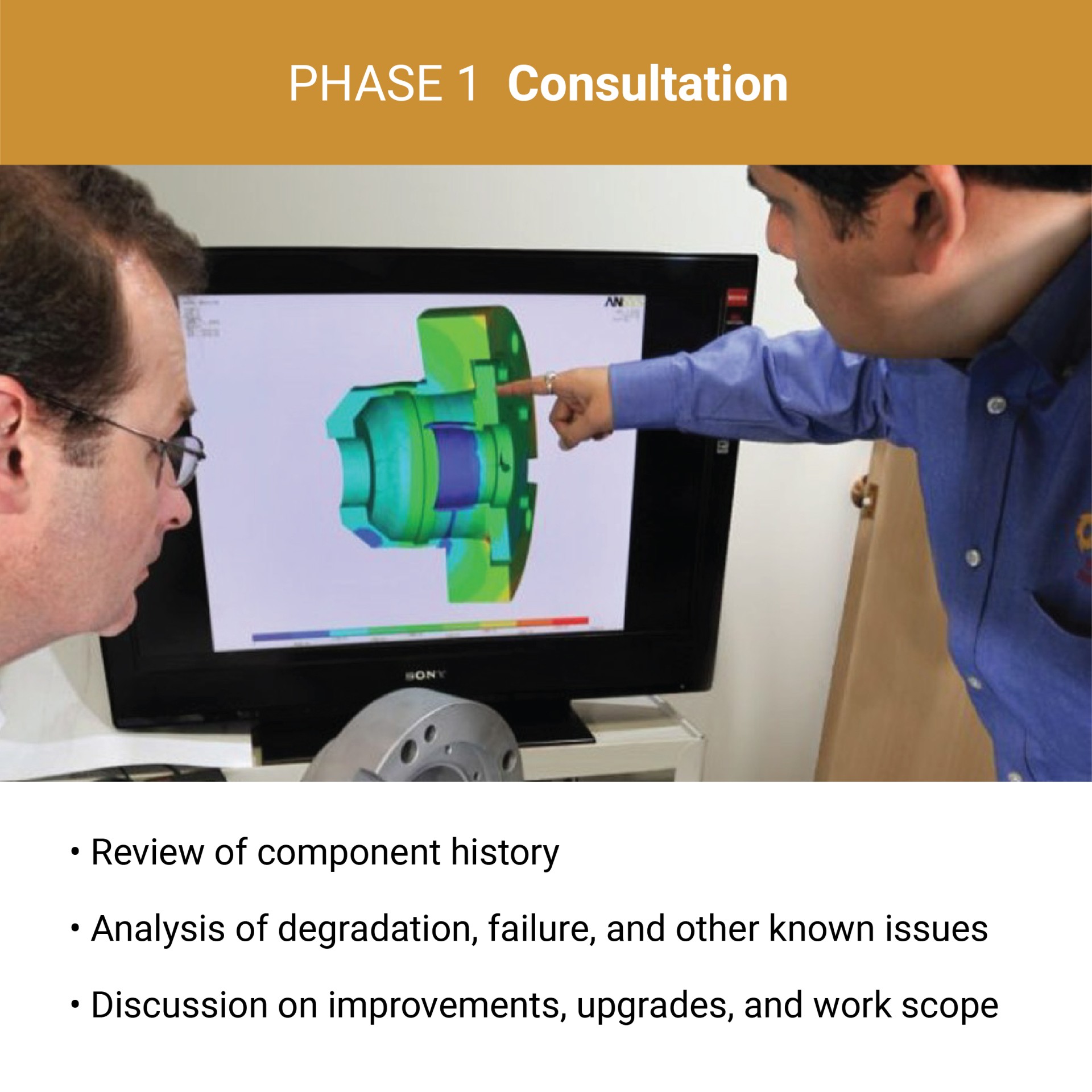
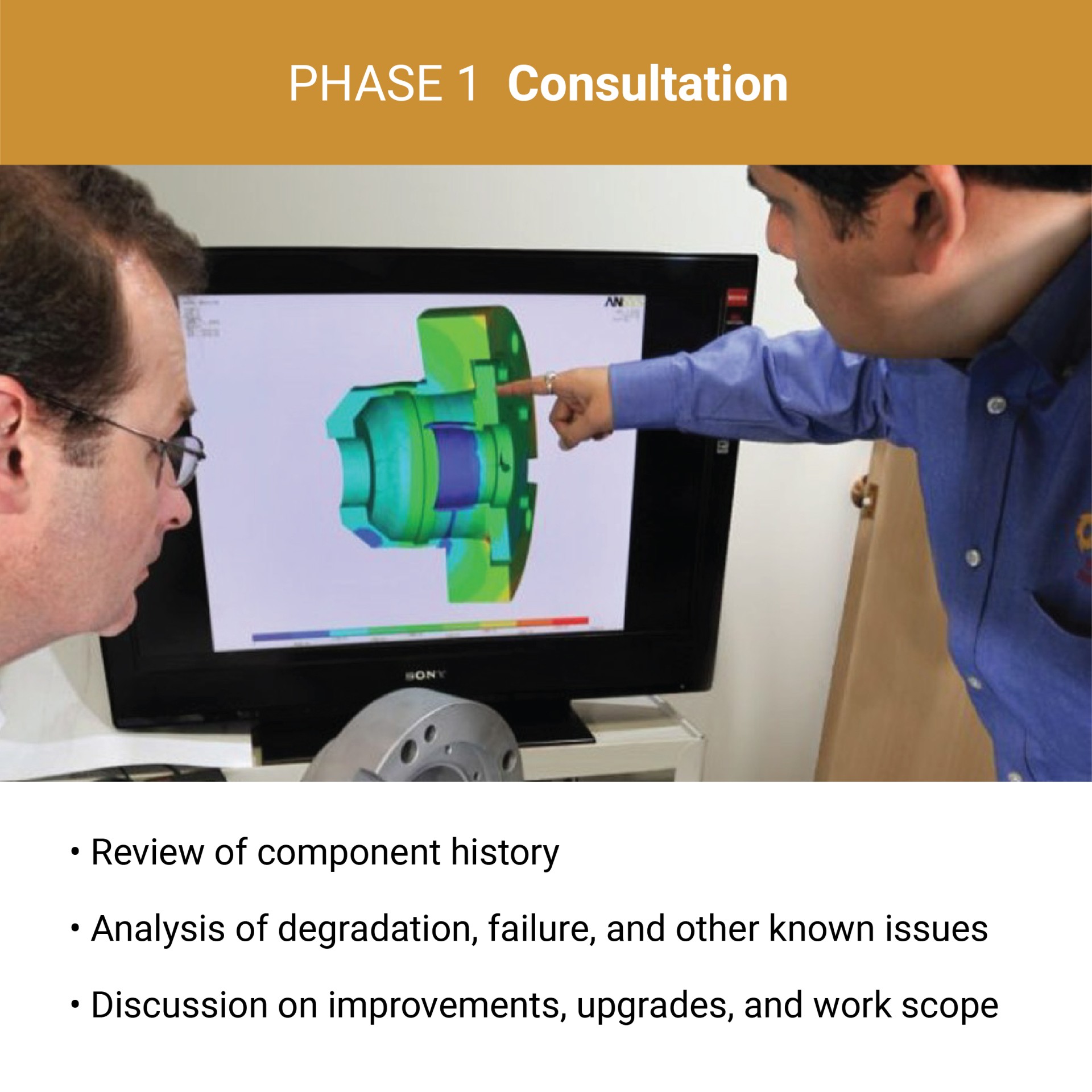
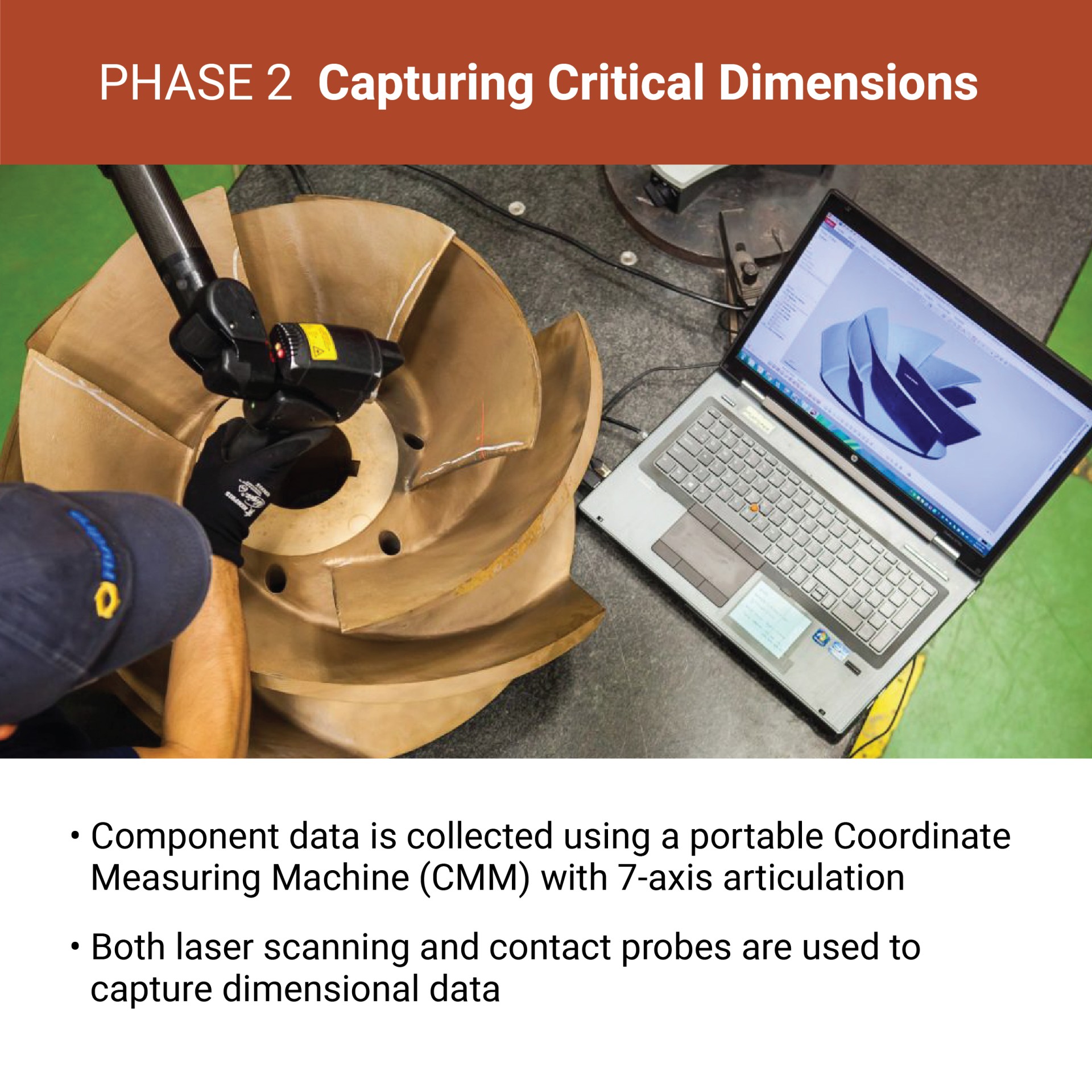
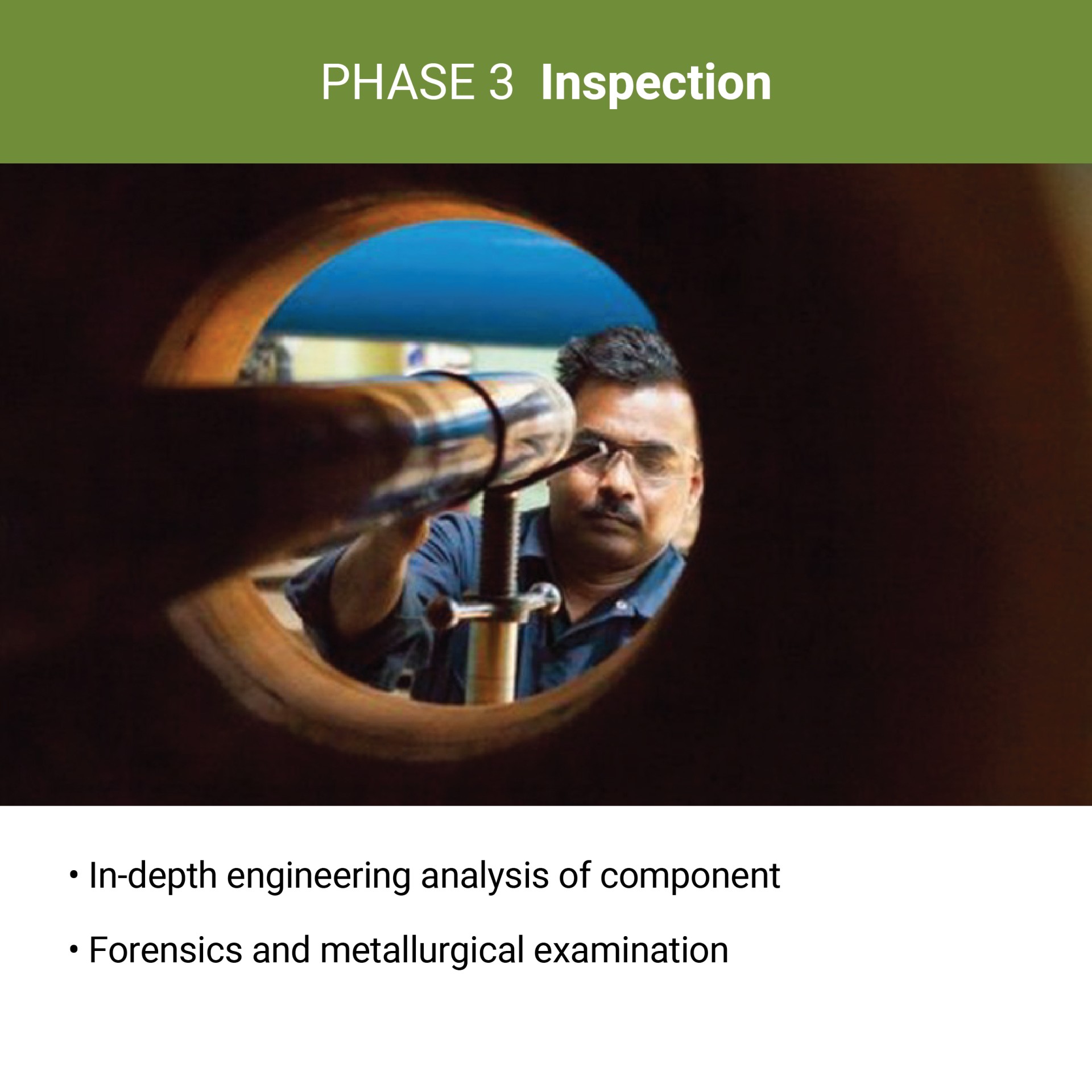
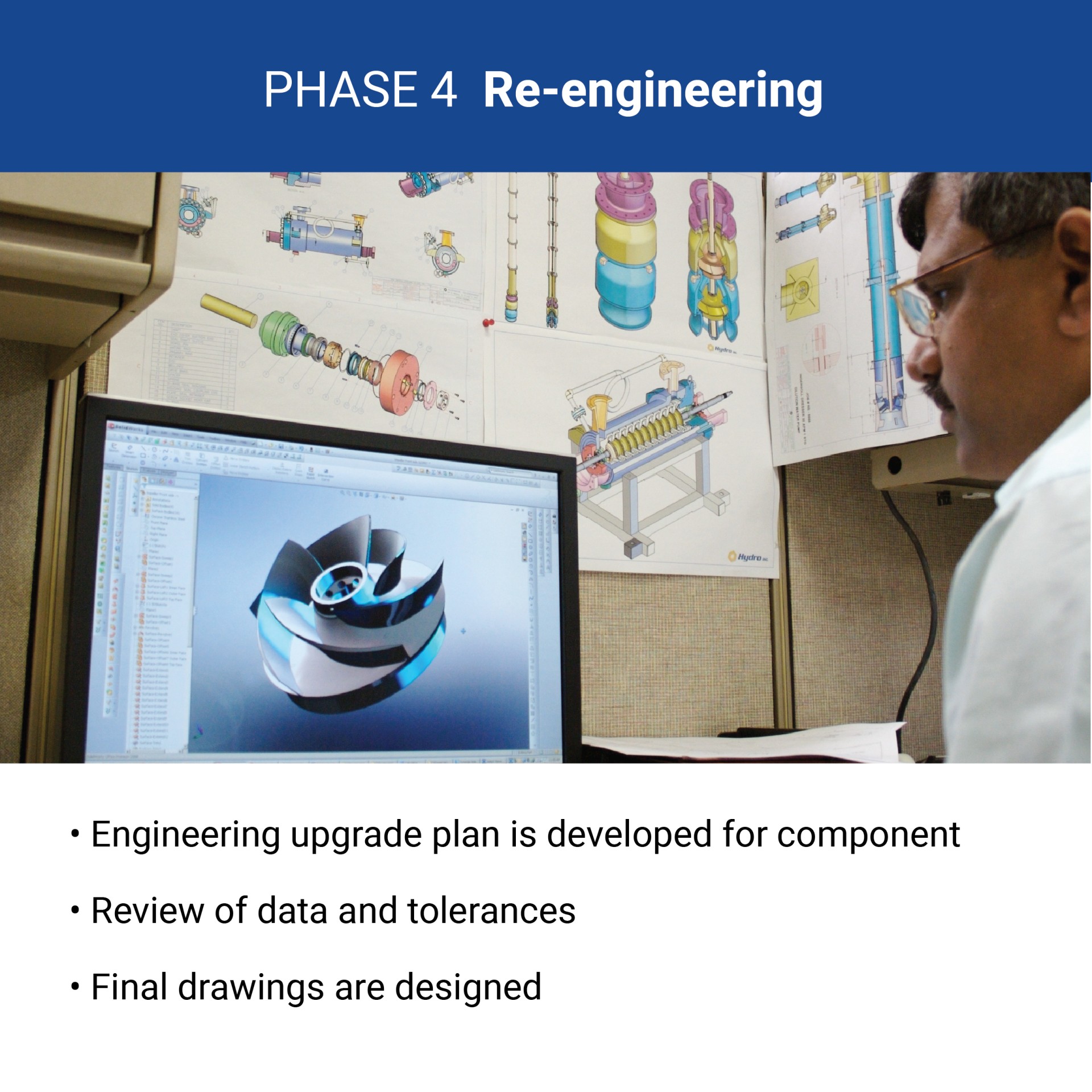
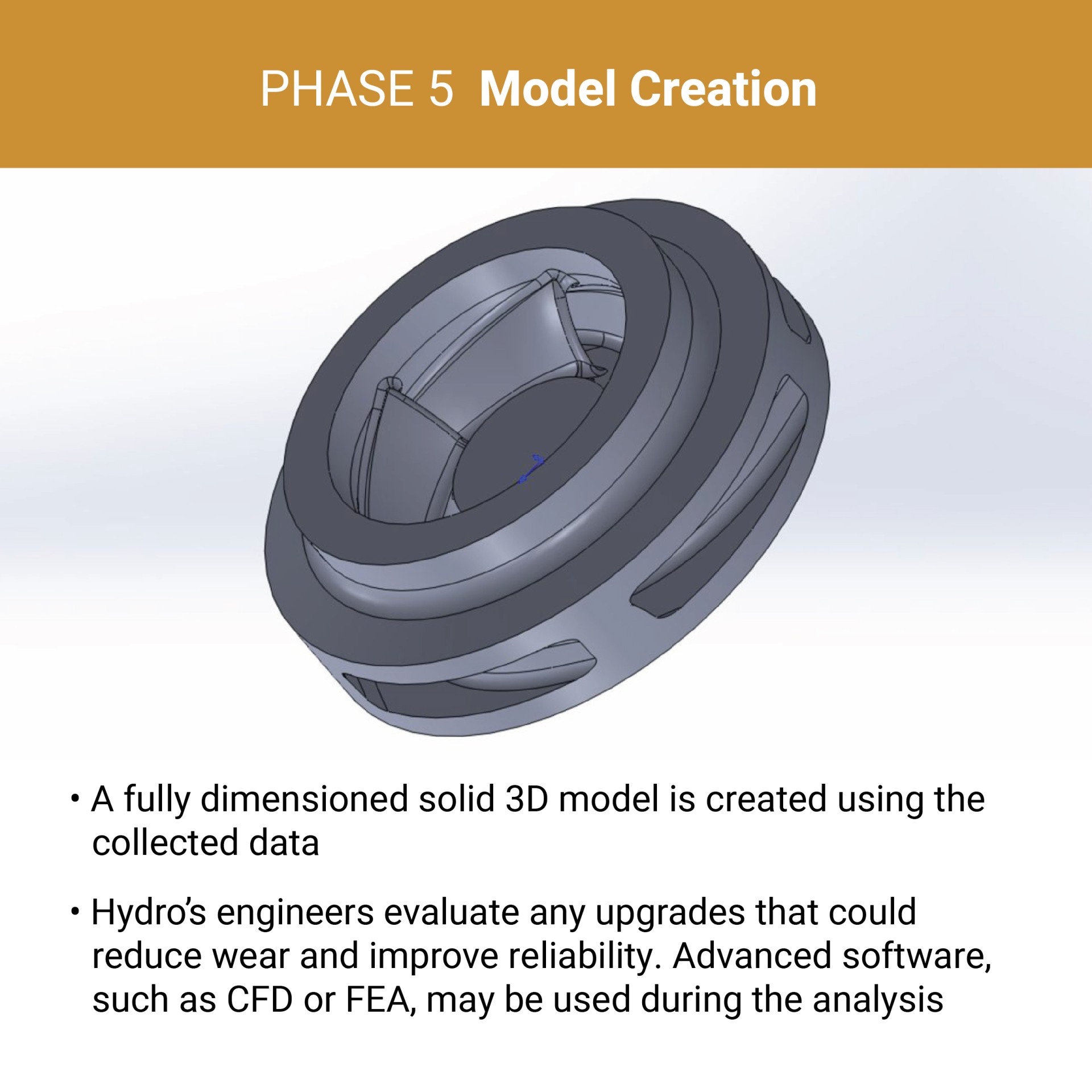
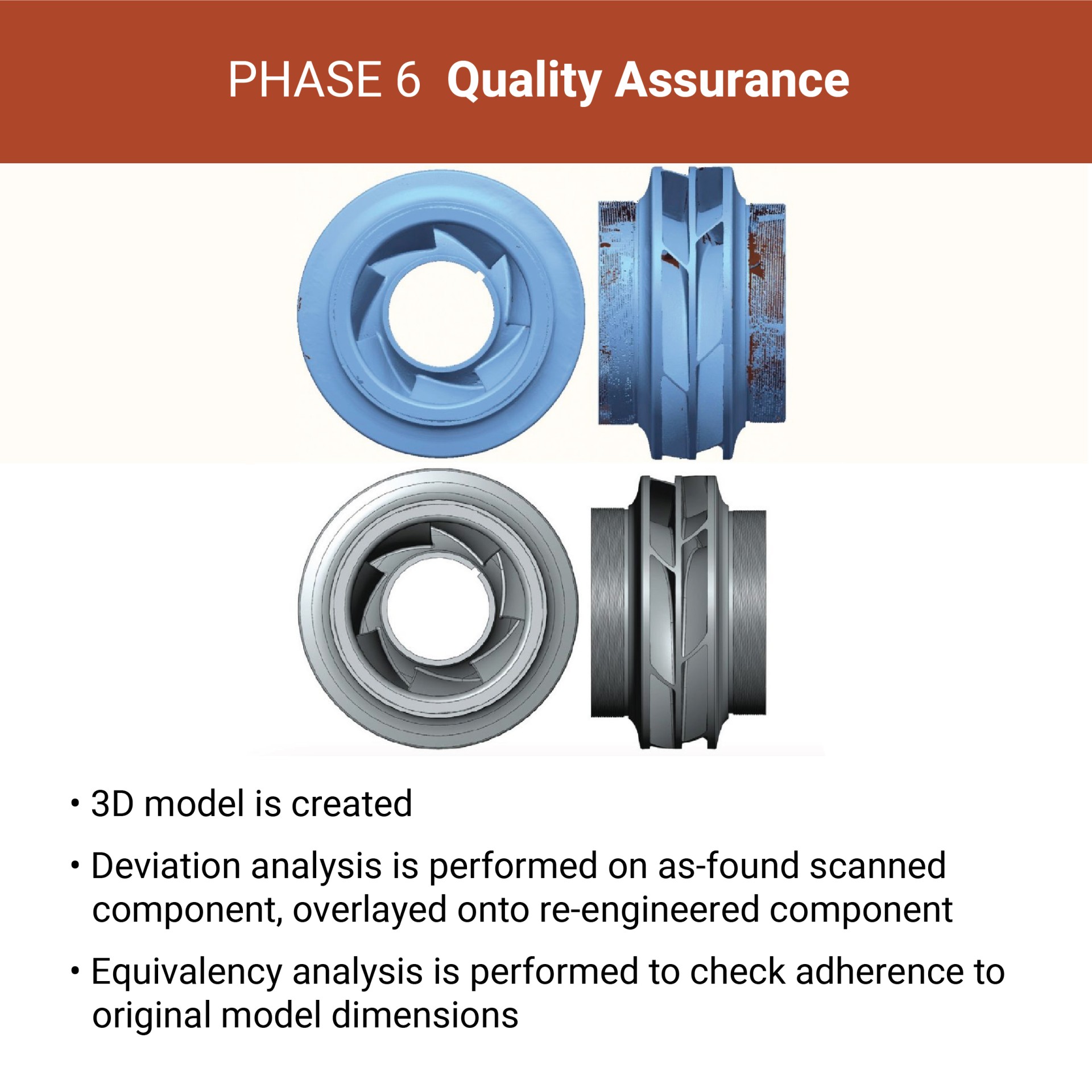
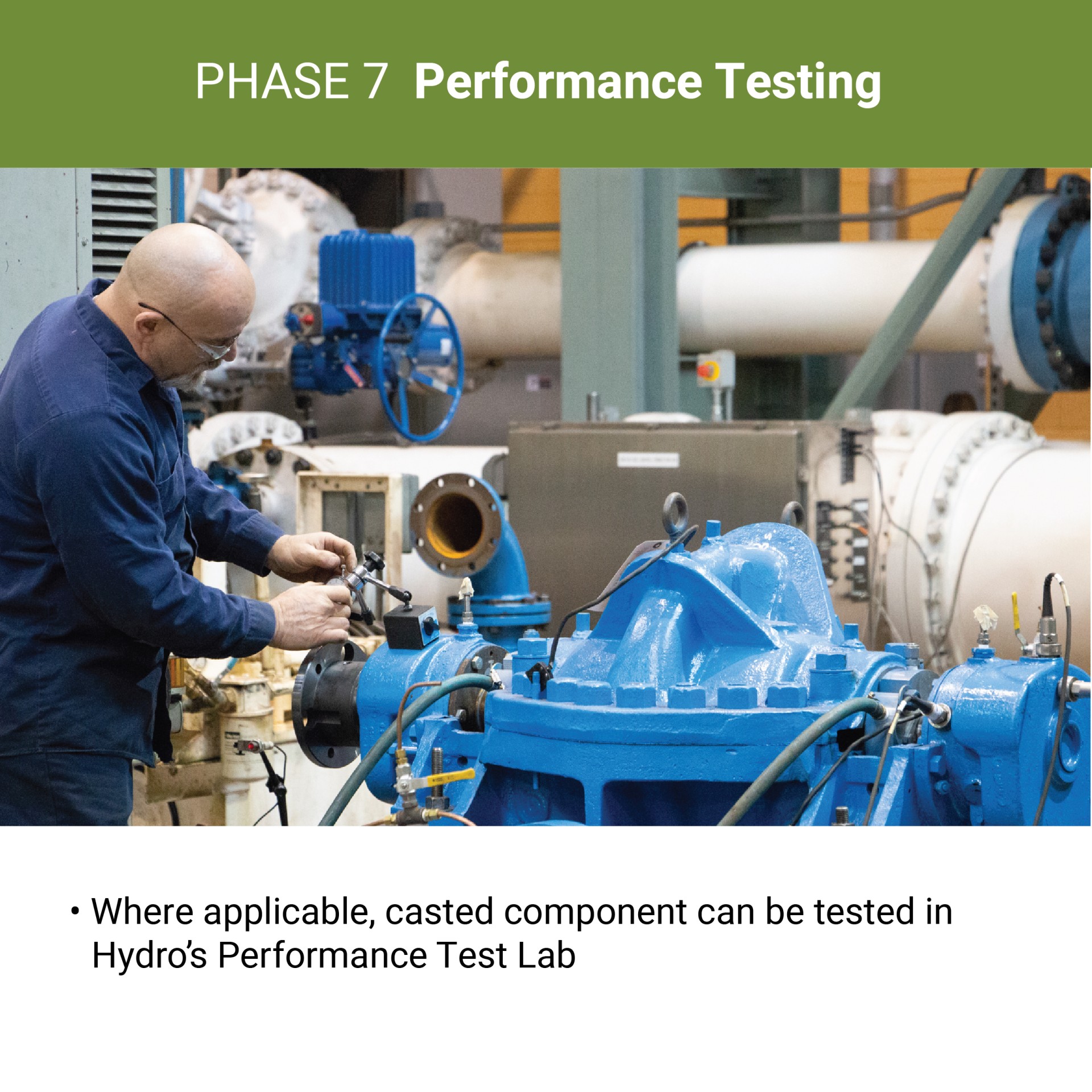
Pump Problems? We've Got This.
At Hydro, it’s about more than quality: It’s about commitment to consistent quality and ensuring that our customers are providing with superior product and optimized mean time between repair for years to come.
Your questions and comments are important to us. Submit a form below, or reach us by phone and we’ll be in touch as soon as possible.