Written by: Jeff Johnson, Hydro, and Bill Rademacher, BP
A refinery’s vertical pump passes the test, verifying its performance before installation.
The rotating equipment engineers at BP’s Whiting Refinery in Indiana approached the support team at a pump service center in Chicago to discuss testing its rebuilt vertical turbine pump in the center’s new 5,000-horsepower test lab. Their pump, a Johnston 40 GMC pump, is one of four pumps used for the refinery’s rainwater drainage and process sewer system. This pump is the first pump in line and has a diffuser built onto the suction bell to direct flow into the pump.
Two other pumps are in line behind this pump and a fourth pump is to the side. All are mounted in a large concrete channel system. BP had implemented a specially designed suction strainer on this pump to minimize potential sump vortexes from entering the pump through the suction side of the impeller.
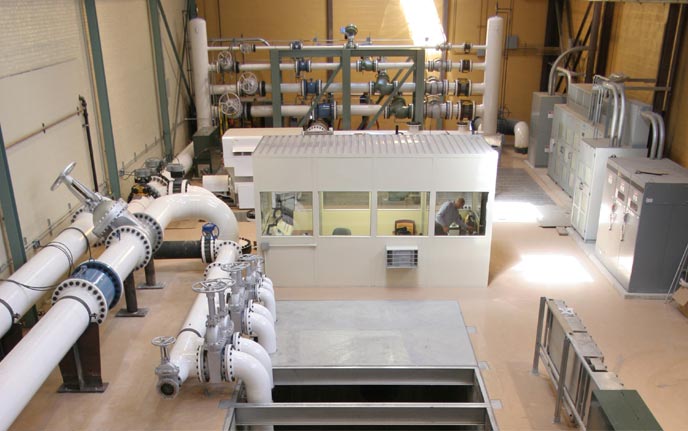
Hydro’s 5000 HP Test Lab in Chicago, IL
This vertical pump had been rebuilt and modified by trimming the impeller and opening the inlet diameter (ID) of the suction bell to improve the flow path characteristics into the impeller eye opening. The refinery wanted verification that the modifications made to the pump resulted in the calculated decreases in horsepower and NPSH required. The goal of the tests, as defined by the refinery, was to determine the operating characteristics, including head (total discharge head—TDH), flow and horsepower, as well as the minimum submergence level of the pump so it could adjust its operating set points and submergence level alarms to avoid cavitation damage.
As the pump service center maintains an “open door” policy, several individuals from the refinery visited the test lab over a two-day period to observe the testing process, which proved to be an educational experience.
-
Johnston 40 GMC vertical pump on the test stand
The Performance Test
Because BP provided the 1,000-horsepower pump motor, the service center engineers were able to set up both the vertical pump and the motor in the test lab. Using this set-up, the service center engineers would be able to help BP obtain an accurate understanding of how their pump would perform in the field.
The service center engineers conducted the performance test and used a validation program to calculate the efficiency using data inputs such as flow, horsepower, barometric pressure, suction level, discharge pressure, temperature and specific gravity of the water, diameters of the piping system and the location of discharge collection points.
The pump’s best efficiency point (BEP) was proved at just under 18,000 gallons per minute, at about 130 feet of head, using about 750 horsepower. Proving the BEP of its pump will enable BP to determine how it should operate the pump most efficiently in the field.
The Minimum Submergence Level
The service center engineers performed a submergence test to show BP where its low sump levels should be set. Cavitation was anticipated at a depth of 39 inches and the service center engineers were able to show the pump’s performance at its lowest submergence point before cavitation could occur, which was 42 inches. The minimum submergence levels were proved so that BP could ensure the best level settings could be achieved in the field without causing damage to the pump.
Ironically, the test pool turned out to be a close replication of the refinery’s sump. This enabled the service center engineers to confirm BP’s suction strainer had been effectively designed. The witnesses to the test could visually see how the suction strainer sheared vortexes that had developed in the sump at low submergence levels.
Lessons Learned
To see further details about Hydro’s 5,000 HP test lab, please visit our Testing Capabilities section.Testing can be an important verification tool for not only ensuring proper performance requirements are met but also to prove mechanical reliability after a pump has been rebuilt. With the ability to configure hundreds of different suction and discharge configurations, the service center was pleased to have been able to work with BP to confirm the performance of its vertical turbine pump. BP has confirmed that the final performance curves are in line with the original equipment manufacturer’s performance curves and that the pump is currently running smoothly.
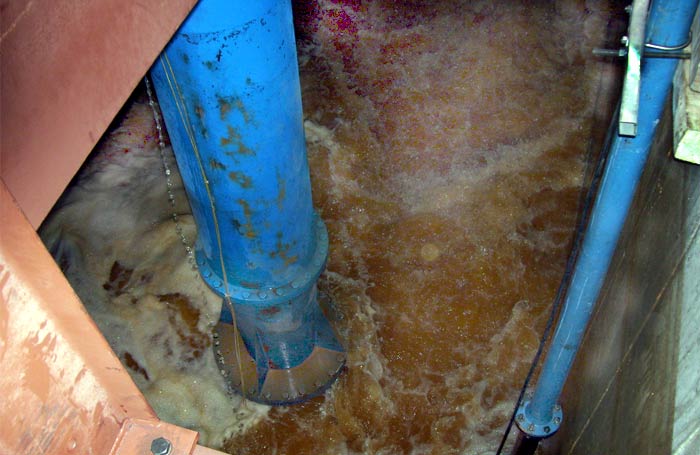
Photo above shows vertical pump operating at lowest possible sump level just before cavitation could occur
Jeff Johnson has 36 years experience in the pump service industry covering numerous markets. Johnson joined Hydro in 2009 and was appointed vice president of Hydro’s Petroleum and Pipeline Division. He was instrumental in the design and construction of Hydro’s new 5,000-Horsepower Test Lab.
With a BS in Mechanical Engineering, Bill Rademacher has been a member of BP’s Rotating Equipment Group at the Whiting Refinery for more than 20 years.