Many pumps in power plants and other heavy industries are designed and custom engineered for specific applications. The repair and servicing of these pumps should also include careful engineering review. Very often, smaller local repair shops attempt to repair these engineered pumps without the input and oversight of an engineer to ensure that the proposed repairs meet the original design’s intent.
When emergencies occur and practical solutions are needed, a service center engineer is invaluable in developing and guiding the pump repair plan. When a plant is down and the pump needs immediate attention, this crucial part of the process may be overlooked or eliminated.
This case history illustrates what can happen when a low-cost repair leads to catastrophic failure and the importance of experienced engineering support from the service center was to return a plant to service.
Circulating Water Pump Fails
Prior to the high-demand summer season, a Midwest plant’s circulating water pump (a 54-in mixed flow pump) failed. When the vertical pump was pulled, it was discovered that both the impeller and suction bell required complete replacement. After checking with the OEM, it was determined that replacing the components would take 8 months. With this pump out of service, the plant was in danger of being derated during the high-demand summer season. The pump had been repaired one year earlier but was no longer under warranty.
At this point, the plant asked a pump service center experienced in engineered pump repairs and upgrades to evaluate the pump and offer a plan for bringing the plant online and running at full rating. The service center’s engineering and operations team evaluated the hydraulic, mechanical, and logistical data and developed a plan to meet the plant’s critical requirements and need for a quick turnaround.
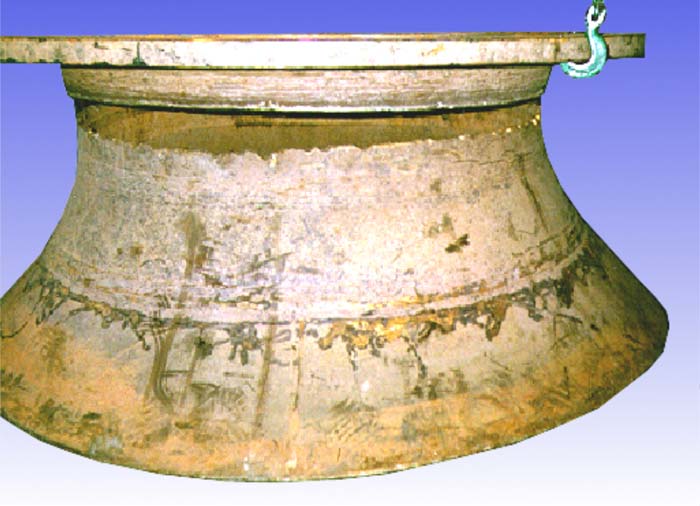
Broken Suction Bell
Failure Analysis
Inspection of the pump revealed that the existing suction bell was not in accord with the pump’s original design. The severely damaged bell had a straight wall (probably a section of standard column pipe was used in the previous repair), which did not meet the contoured wall of the original design. The straight-wall did not have the proper contour to match the impeller profile. The reduction of the gap between the impeller and the wall of the suction bell affected the pump’s flow and served as the basis for poor overall performance. Moreover, the wall thickness of the existing bell was only 0.080-in. In some areas, the wall had been further weakened by improper machining, which reduced the thickness of the wall to only 0.020-in.
The service center engineers believed that the improper contour and reduced wall thickness had significantly weakened the component’s strength. It was likely that higher than normal vibration had affected the weakened component, causing the fabricated bell to break apart into two sections while in operation. This failure severely damaged the impeller, almost completely destroying the impeller blades.
Engineering Solutions
When the pump arrived at the service center, the suction bell was in two pieces. A new cast bell could not be procured within the time frame required by the plant. Employing proven engineering principles and geometry, the service center’s engineers designed two separate cones that would be welded together to form the new suction bell. For durability, the material was upgraded from cast iron to a specially rolled stainless steel material to meet the pump’s configuration requirements.
The impeller proved an even greater challenge. The existing impeller blades had been virtually destroyed when the suction bell broke into two pieces. As a result, the hydraulic profile was not available. In addition, the impeller had been cast in a special high lead content bronze, which was not available from local foundries. The use of special bronze alloys was common 40 to 50 years ago when the pump was designed and manufactured.
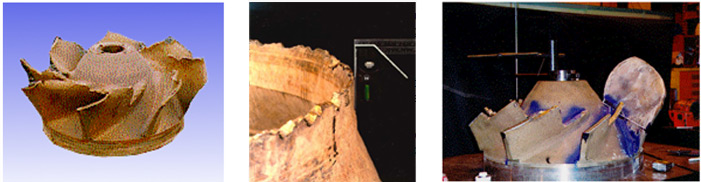
(Left) Impeller with broken blades (Middle) Suction Bell straight wall (Right) Old Vanes removed from Impeller
The service center’s hydraulic design engineers analyzed the performance requirements of the original design using CFD (computational fluid design) and data that was available from the existing impeller to recreate the impeller’s hydraulic profile. A CAD drawing was developed and electronically transferred to the foundry for the mold used to cast the impeller vanes.
Because the engineers’ solution involved welding new blades to the existing impeller hub, it was essential to manufacture the blades from precisely the same material as the hub. A metallurgical analysis had to be performed on the original impeller so new vanes could be cast of the special bronze alloy material. The service center sent samples of the unusual bronze material out for analysis and worked with a smelter to duplicate the original material composition exactly. The ingots they produced were then transferred to a foundry where they were used to cast the newly designed blades. What remained of the old blades were carefully plasma arc removed. The new blades were then welded (using base metal welding material to ensure a high degree of strength) to the original impeller hub.
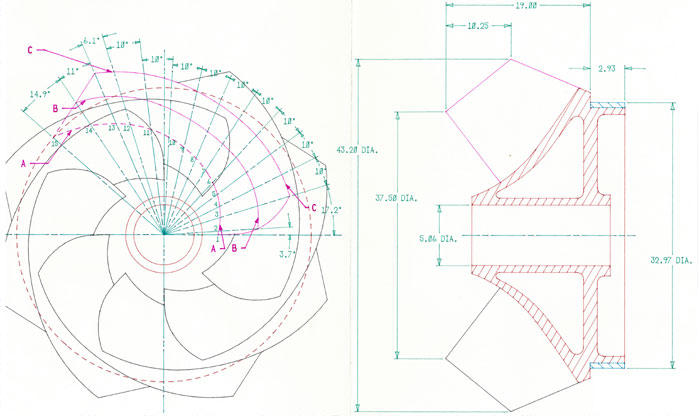
Diagram for the Impeller
The service center manufactured a special fixture to space out the vanes, align them to the hub, and to orient precisely during the welding and heat-treating cycles. To aid the machining, special jigs were designed and manufactured to hold the hub true and concentric to the engine lathe’s center. In addition, a special balance arbor was also manufactured to facilitate dynamic balancing to the engineer’s strict balancing procedures and standards. In this instance, the impeller was balanced to 4W/N.
Throughout the job, the service center maintained daily communication with the plant-advising them on any problems, the proposed solutions, and the expected project completion date. Involving the plant was critical to the overall project. The project was successfully completed within 7 weeks, the plant’s delivery requirements were met and the pump was in service for the critical summer season.
Lessons Learned
While it is always important to watch costs, it is also important to “vet” your service center when dealing with engineered pumping equipment. Make sure the engineers have the knowledge and experience to analyze the problem and provide a quality solution based on sound engineering analysis and practices.
A low-cost solution, which departs from the integrity of the pump’s design and is not supported by a thorough engineering review, may end in catastrophic failure and an unplanned outage.
A lack of engineering input and review can drive up total costs and, more importantly, can result in unplanned outages, which affect plant costs and revenues. This plant estimated that direct costs alone exceeded $1.5 million