Many pumps in power plants and other heavy industries are designed and custom engineered for specific applications. The repair and servicing of these pumps should also include careful engineering review. Very often, smaller local repair shops attempt to repair these engineered pumps without the input and oversight of an engineer to ensure that the proposed repairs meet the original design’s intent.
When emergencies occur and practical solutions are needed, a service center engineer is invaluable in developing and guiding the pump repair plan. When a plant is down and the pump needs immediate attention, this crucial part of the process may be overlooked or eliminated.
This case history illustrates what can happen when a low-cost repair leads to catastrophic failure and the importance of experienced engineering support from the service center was to return a plant to service.
Circulating Water Pump Fails
Prior to the high-demand summer season, a Midwest plant’s circulating water pump (a 54-in mixed flow pump) failed. When the vertical pump was pulled, it was discovered that both the impeller and suction bell required complete replacement. After checking with the OEM, it was determined that replacing the components would take 8 months. With this pump out of service, the plant was in danger of being derated during the high-demand summer season. The pump had been repaired one year earlier but was no longer under warranty.
At this point, the plant asked a pump service center experienced in engineered pump repairs and upgrades to evaluate the pump and offer a plan for bringing the plant online and running at full rating. The service center’s engineering and operations team evaluated the hydraulic, mechanical, and logistical data and developed a plan to meet the plant’s critical requirements and need for a quick turnaround.
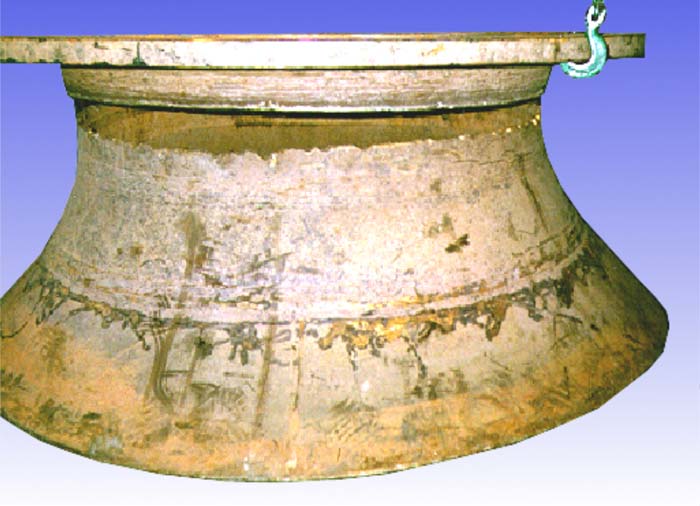
Broken Suction Bell