Creative approaches that extend beyond original designs, standard tools, and traditional engineering practices can provide significant savings and higher reliability of pumping equipment. For example, in one such situation, the casing of a charging pump at a European nuclear plant had been over-pressurized and needed to be refurbished. Not only was the pump service radioactive, but the casing was also found twisted with its internal components unable to properly fit into the casing, and the machined surfaces out of alignment.
The original equipment manufacturer (OEM) of the pump stated that they could not repair the casing and that the only option was to purchase a new one. The nuclear plant’s engineers approached Hydro, Inc., a global aftermarket pump service provider, for assistance in finding a spare casing. When no spare was found, Hydro initiated a more detailed discussion with the plant about refurbishing the casing.
Hydro’s team inspected the pump, the casing, and the internal element and explored all possible options (Figure 1). Hydro was able to find an inventive solution by machining the casing in the contaminated state and developing creative methods to guarantee a proper fit-up when the casing repair was completed. Despite the OEM suggesting a new pump be purchased, the service provider was able to find an innovative and cost-saving way for the plant to repair the casing and reduce downtime.
The Challenge
The nuclear plant had ordered a new casing. However, the long lead time from the OEM added additional risk because the plant was running without a backup.
With the customer’s needs for a timely resolution in mind, Hydro suggested exploring options for repairing the casing. Although a 3D scan of the casing was provided, Hydro needed a more detailed approach to guarantee a successful repair. The initial step was to examine the equipment first-hand with precision tools, shims, and precision straightedge to measure flatness and geometry (Figure 2). A Hydro inspector traveled to the European nuclear plant and conducted a thorough inspection of the internal element and casing. With a complete report of the geometric data, Hydro’s engineering team considered innovative options and determined that the casing could be repaired.
The casing was contaminated with radioactive material, which presented an additional challenge. Because the pump had a unique configuration, it could not be free released.
The size of the casing and the machining requirements meant the work needed to be done at a facility with a larger sized machine tool. Hydro proceeded to talk to three major contaminated pump service facilities, i.e. hot shops, but these facilities do not usually have the proper tooling to meet the provider’s precision standards for managing the contamination and the repairs for this repair. Fortunately, Hydro had the necessary machine tool, which was not found in any of the other dedicated contaminated pump repair facilities.

Figure 2: Hydro’s engineers measured flatness during the inspection using precision straight-edge tools.
Hydro’s engineering team needed a creative solution. The need for precision equipment and hot shop operation was integral to the success of the repair as Hydro had to be certain that the casing and internal element would fit perfectly at the plant in Europe.
The Solution
The only way to accomplish the repair was by arranging for a Radioactive Material License to be transferred to Hydro’s facility. They fenced-in an area so the entire workspace would be protected. Workers were subject to hazmat conditions and wore proper personal protective equipment. Four technicians were trained with an emergency set-up. A licensed certified health physics project manager was on-site to oversee the project the entire time to ensure protection from contamination.
The casing was sent to a nuclear contamination service provider for as-found radiation and some initial decontamination and then was sent to Hydro’s facility to perform the repairs. The nuclear plant sent their pump specialist, QA specialist, and lead machinist to the United States to oversee the pump repair. The emergency repair required two 12-hour shifts of machining for six days to successfully repair the casing.
An interesting part of this complex project was the verification of the final machining dimensions and the quality of the machining to make sure the rotor would fit into the casing. Hydro’s engineering team did not want to take any chances of the rotor not fitting properly in the casing when it was returned to the nuclear plant, so they developed a unique approach to verify these critical dimensions in the casing.
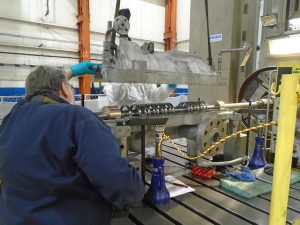
Figure 3: The pump was assembled with the mock-up rings to verify proper fit-up.
During their initial inspection at the nuclear plant, Hydro measured the relevant components of the rotor so they could create mock-up wear rings. These rings are the stationary components that support the rotor in the casing. If the mock-up rings matched exactly, then the rings could be manufactured to ensure the repaired casing would fit properly.
The precision mock-up rings were used to measure concentricity and to ensure that the rotor would fit properly in the casing when assembled (Figure 3). The precision mock-up rings were manufactured by Hydro.
The Results
Hydro performed all of the proper protection of the machine tools, as well as trained four machinists and inspectors for the radioactive work environment. This was all done under emergency conditions and in parallel with other tasks to save time. The casing was machined successfully in six days, on time, and the entire project, from receipt of the pump in the US to its return to the nuclear plant, took only two weeks.
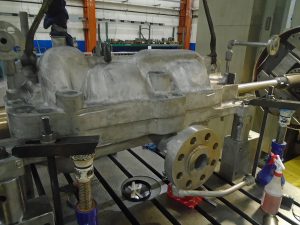
Figure 4: The casing after being completed and machine; ready for shipment.
Hydro performed a final cleaning and passivation check to ensure that no iron contaminants were found in the newly repaired casing. With negative results on the passivation check, Hydro was able to ship the casing back to Europe (Figure 4). The customer was impressed with the innovative approach and with the management of the many details in this unique project scope. The creative approach saved the nuclear plant time and money, while also reducing their risk.
Highlights of the project include:
- The development of an original approach that expedited a solution to alleviate the nuclear plant from running at risk.
- The creative approach led to a unique method of ensuring the fit-up of the rotor components to the casing.
- Because of the unique aspects of the project scope, close coordination, and project management were significant for the complex variables.
- The pump is a Safety-Related ASME-N Stamp pump, which requires stringent and specific compliance rules.
Hydro’s core competencies are related to pump services. Hydro approaches each repair project from an engineered and innovative standpoint. Hydro’s expertise is in repairing critical pump components to the same, if not higher quality, and in doing so improving the reliability of pump performance.
Source: https://www.neimagazine.com/features/featurerefurbishing-a-contaminated-nuclear-casing-8452532/