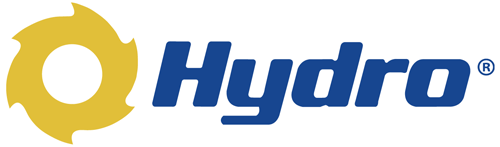

Critical Pump Testing
Optimum Performance
FAQ:
What kinds of pumps can Hydro test?
Hydro is capable of testing horizontal, vertical, submersible, and some reciprocating pumps. We can test pumps up to 5,000 HP and achieve a maximum flow of 42,000 gpm. All testing is completed in accordance with HI 14.6-2011 and API 610 (or other relevant standards such as ASME and ISO).
What is the purpose of pump testing?
The purpose of a pump performance test is to ensure that the actual performance of a pump achieves the desired operating condition and/or original design condition (i.e. differential head at a given flow capacity).
The test can be applied to a new pump, refurbished pump, or re-engineered pump with the focus being on reliability, assurance of meeting the required operating conditions, and measuring the actual changes in performance if a change was made. For example, in an energy optimization project, a pump may be designed to achieve a higher efficiency to save on the operating cost of the unit. A performance test can be completed to validate the engineering and design. If a test is not completed, the end user may be going into operation with only the design engineering and reputation of the vendor to count on.
The test can be applied to a new pump, refurbished pump, or re-engineered pump with the focus being on reliability, assurance of meeting the required operating conditions, and measuring the actual changes in performance if a change was made. For example, in an energy optimization project, a pump may be designed to achieve a higher efficiency to save on the operating cost of the unit. A performance test can be completed to validate the engineering and design. If a test is not completed, the end user may be going into operation with only the design engineering and reputation of the vendor to count on.
What does it mean to be a Hydraulic Institute (HI) Approved Test Lab? When did Hydro receive this accreditation?
This accreditation recognizes Hydro’s ability to perform pump testing to the 40.6 Pump Efficiency Testing Standards that aim to address the new United States Department of Energy (DOE) testing standards for pumps. Hydro was the first pump test facility to receive this recognition and was awarded the accreditation in September of 2015. Check out this article for more information on the achievement.
What is the end result of a Certified Performance Test?
The end result of a Certified Performance Test is a certified performance curve showing the differential head versus flow capacity, input power versus flow capacity, and efficiency versus flow capacity curves over the total range of flow capacity for a given pump. This curve is generally presented at the nominal operating speed of the pump, but can also include additional impeller trim performance curves or additional operating speed curves for the same pump.
How does Hydro perform Net Positive Suction Head Testing?
Hydro has a vacuum pump connected to the above ground suppression tank used for horizontal pump testing. The vacuum pump can be used to lower the Net Positive Suction Head Available (NPSHA) until the pump reaches cavitation (3% head loss) at a given flow rate. Hydro can also perform NPSH testing on vertical pumps in most cases.
Do you perform Vibration Analysis?
Hydro has a 16-channel vibration analyzer capable of measuring vibration amplitude, frequency, waveform, and phase for 16 channels simultaneously. In addition to condition monitoring of tested machinery, further analysis can help in addressing existing machine issues, resonant frequencies, critical speeds, and machine improvement possibilities.
Can you perform variable speed testing?
Yes, we have several Variable Frequency Drives (VFDs) of different horsepower ratings that allow us to control the speed of the motor. This allows for additional performance curves at varying speeds to be tested instead of calculated using the Affinity Laws, critical speed testing, and the simulation of additional off-design conditions.
Can you perform a Critical Speed test? What is that exactly and how is it tested?
Yes, Hydro utilizes state-of-the-art vibration analysis techniques to identify critical speeds present below the maximum operating speed of the pump. In the field, a pump can be driven by a Variable Frequency Drive (VFD), which acts to regulate the pump’s speed in an effort to reduce power consumption and wear on the pumping system during times of lower pumping demand. If a critical speed was present below the maximum pump speed, the pump would be subject to damaging resonant vibrations as it passes through or operates within 10% of the critical speed. By identifying the critical speed in a controlled test environment, the customer is able to avoid operating the pump at or near the critical speed thereby ensuring safe pumping conditions.
Can you run an endurance test?
Yes. The above ground tank and vertical pit can be connected to cooling tower or refrigeration systems that allow for extended endurance tests.
What is LabVIEW?
LabVIEW (short for Laboratory Virtual Instrumentation Engineering Workbench) is a platform and development environment for a visual programming language. LabVIEW is commonly used for data acquisition, instrument control, and industrial automation. LabVIEW will record performance parameters like pressure, flow, power, and so on, and record all the test data used to create the performance curves of the pump. Hydro has a custom built pump test program based on the flexible platform provided by LabVIEW. It is a state-of-the-art test program.
Does Hydro account for measurement uncertainty?
Hydro measures uncertainty at every test point recorded. Without this analysis we would be unable to truly quantify the accuracy of the test results. In addition to random measurement fluctuations, known instrument calibration uncertainty is also included in the final calculation.
How do you measure flow capacity?
Flow is measured using calibrated magnetic flow meters. The specific flow meters for a given test is selected to optimize accuracy and reduce uncertainty in the test results. Depending on the expected flow velocity, the specific magnetic flow meter(s) will be selected automatically through the data acquisition system. The highest flow rate we can measure is 42,000 gpm.
What type of instrumentation do you use to measure pressure?
Pressure is measured by using calibrated pressure transducers. The specific transducers used for testing are sized for the expected pressure range of the pump and mounted to the suction and discharge piping per Hydraulic Institute 14.6-2011.
How do you measure pump input power?
Whenever possible, a calibrated torque meter or strain gage is used to measure input power to the pump. For full train, close-coupled, and/or submersible tests that do not allow space for either a torque meter or strain gage, a calibrated watt meter is used to determine input power. In addition, voltage, current, power factor, and related temperatures are measured when required.
How many motors do you have?
Hydro has many calibrated test motors of various sizes intended to cover various pump designs in the aftermarket. The largest motors are 2-pole and 4-pole 5000 HP motors. Our largest vertical motor is a 4-pole 2000 HP motor.
How do you adjust inlet/outlet piping to accommodate various pump sizes and configurations?
Horizontal pumps are set up on a 20’x30’ baseplate plate with movable pump and motor supports. Piping is then installed to the pump and existing manifold connections, which range from 4” to 30”, which allows for a quick and accurate installation. The large size of the baseplate allows for multiple pumps to be installed simultaneously, reducing time between tests and optimizing the piping configuration.
Similarly, vertical and submersible pumps are installed and connected to existing piping configurations in order minimize setup time and ensure an accurate test.
Similarly, vertical and submersible pumps are installed and connected to existing piping configurations in order minimize setup time and ensure an accurate test.
What are inlet and outlet sizes for the tank and will there be vortex in the tank?
The discharge inlet is 24” and the suction outlet is 30”. The tank is designed with special plates inside to suppress vortex formation.
How big is your above ground tank?
The above ground tank is 48 ft. long with a 12 ft. diameter and has the capacity to hold approximately 38,000 gallons of water. The tank can be pressurized up to 100 psi to match a field suction condition. The tank pressure can be depressurized with a vacuum pump.
How big is your vertical pit?
Our pit is approximately 48 ft. long with varying depths. The deepest section is approximately 35 ft. deep with a 10 ft. diameter section for the lowest 20 ft.