Engineered
Parts Solutions
Hydro’s engineering experience, use of the latest design technologies, and quality manufacturing processes enable us to support emergency parts requirements and provide component repeatability with a high degree of accuracy. When you require a cast part and are facing a long lead time, Hydro can meet your needs in a reduced time frame. We’re on it.
We Are Pump Experts
Hydro Parts Solutions supports all Hydro’s service centers and customers in casting difficult-to-source parts, such as impellers, diffusers, discharge heads, casings, bowls, suction bells, and much more. Hydro Parts Solutions can fulfill casting needs for customers without long wait times, compromised quality, and high costs.
As the need for cast parts became a need for finished, high-quality products, many advanced tools were added to the shop. Utilizing state-of-the-art technology such as 3D printing and design, Hydro Parts Solutions established itself as a center that possessed sophisticated casting capabilities with a delivery time that beat OEMs by weeks.
Global Network. Local Heart.
As part of the Hydro network, Hydro Parts Solutions has access to Hydro’s extensive resources, including the global engineering team, performance test lab, and capability in advanced modeling, such as CFD, modal analysis, and FEA. Hydro’s strict process control procedures and data management system allow HPS to ensure consistent quality and catalogue part data for future use.
Although Hydro has an extensive global reach, Hydro Parts Solutions is still local at heart. HPS prides itself in its flexibility and responsiveness. We understand the importance of transparency and communication for our customers, especially when a part is needed for an emergency repair or short turnaround.
Combining Experience & Technology
When it comes to the casting process, our Hydro Parts Solutions team uses their casting and foundry experience to provide a mold package that minimizes the risk of casting flaws. Using advanced software, they model the solidification of the alloy in the mold to ensure a quality product in the first pour. Their strong relationship with foundry partners allows them to provide oversight and inspection on-site during the casting process.
Hydro Parts Solutions has invested in the technology necessary to provide single-use molds manufactured through computer-aided machining and 3D sand printing. The ability to produce a single-use mold can be very helpful in an emergency when the part needs to be expedited or in cases where the part is obsolete and no longer supported by the original manufacturer.
Engineering Makes All the Difference
To achieve the best result for our customers, expert engineering is supported by the latest technology and proven process control procedures.
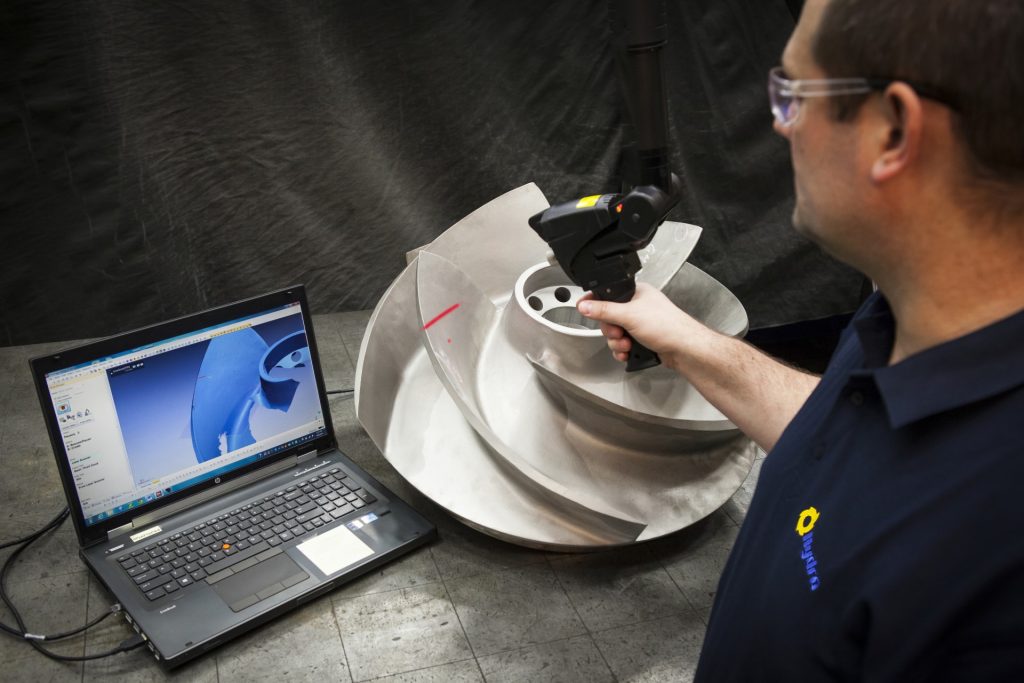
- Component data is collected using a portable Coordinate Measuring Machine (CMM) with 7-axis articulation
- Both laser scanning and contact probes are used to capture dimensional data.
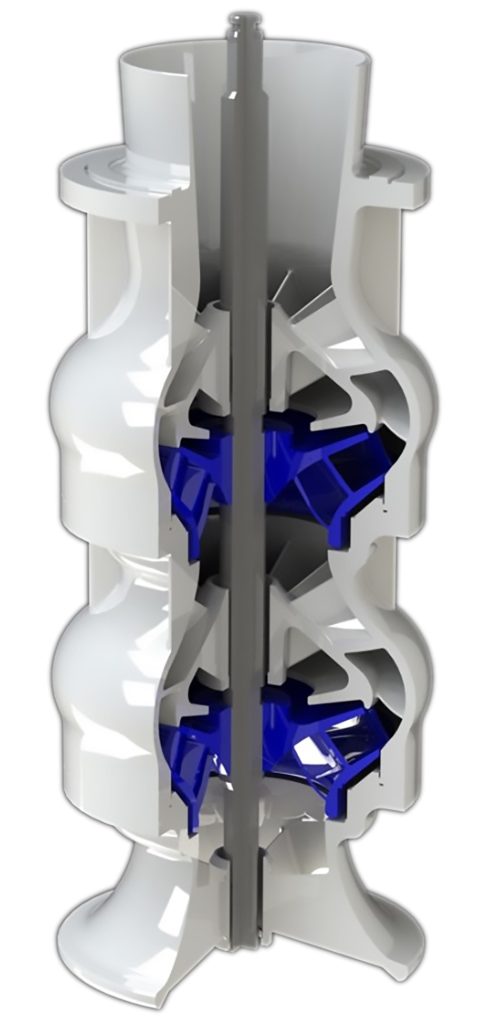
- A fully-dimensioned solid 3D model is created using the collected data
- Hydro’s engineers evaluate any upgrades that could reduce wear and improve reliability. Advanced software, such as CFD or FEA, may be used during the analysis
- After design verification, the 3D model is finalized
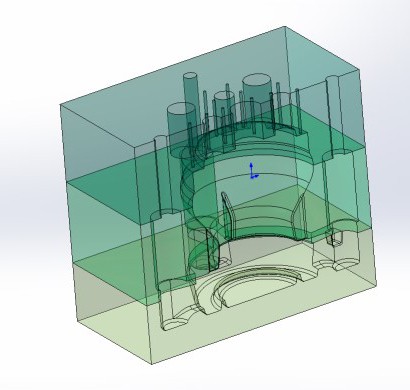
- Casting model is created with allowance for machining stock
- Mold design is started by modeling gating and risers
- Solidification analysis is completed to understand shrinkage, manage temperatures, and draw hydrogen gas out of the casting
- The mold and core package design is verified and digitally assembled
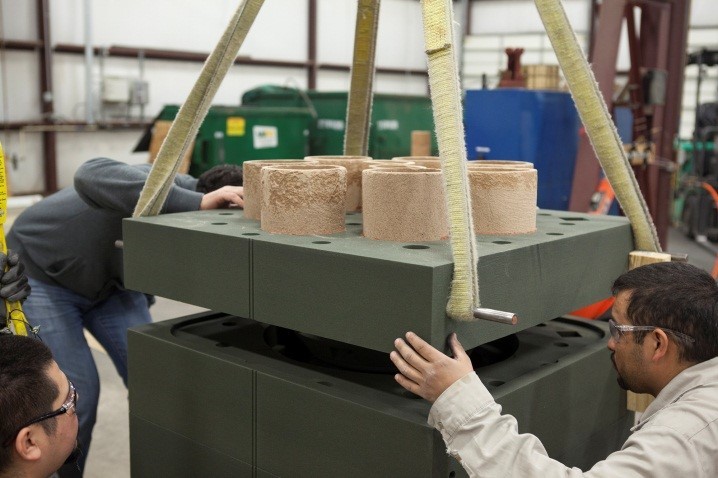
- Computer-aided machining and/or 3D sand printing is used to manufacture the 3D molds and cores
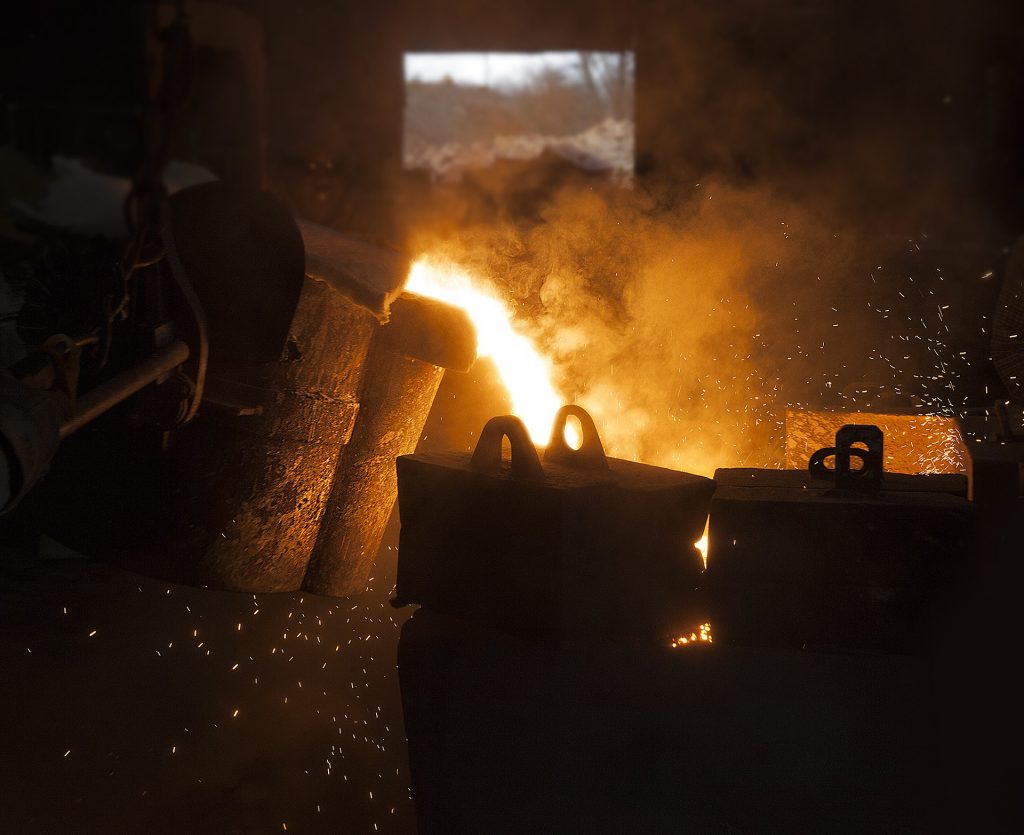
- High content zircon wash is applied on all surfaces to improve surface finish
- Package is assembled and pour is completed
- Part is poured, broken out of the mold and cleaned
- Cast part is dimensionally inspected by Hydro’s engineers.
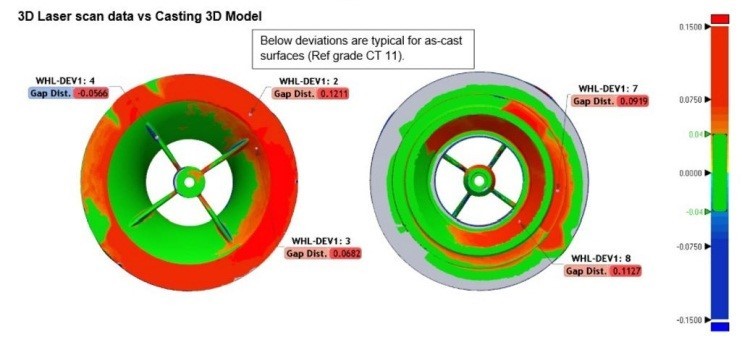
- Casting is inspected for defects
- 3D model of the cast part is created and compared to the original model to validate the casting dimensions before it is released for machining
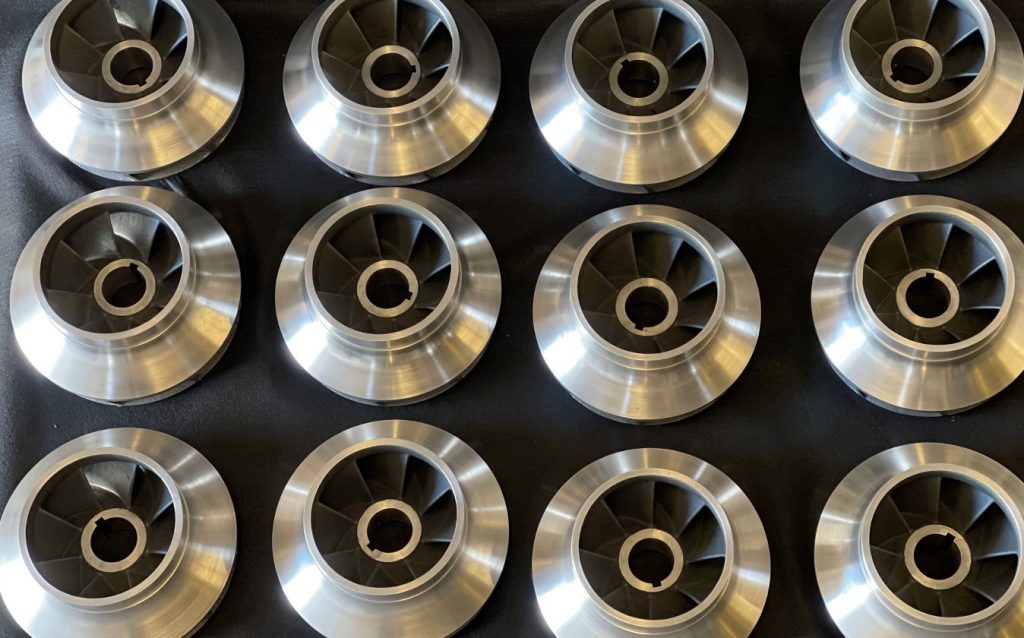
- After casting approval, final machine drawing is produced and approved
- Machining, drilling, surface finish and dressing is performed
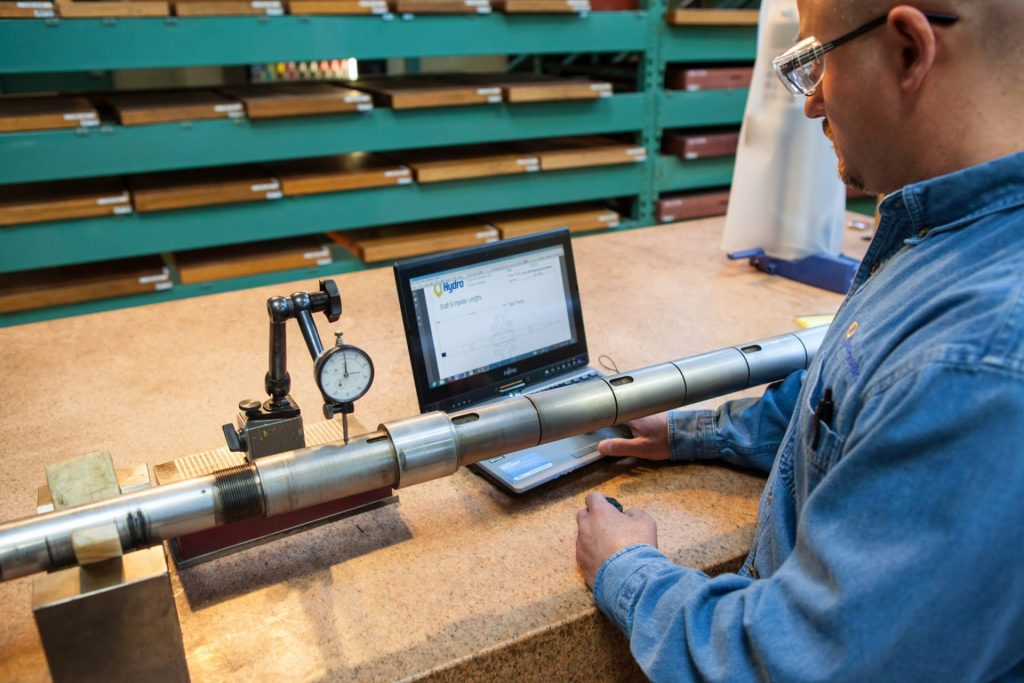
- Hydro’s Quality Assurance Team inspects machined component
- Equivalency analysis is performed to check adherence to original model dimensions
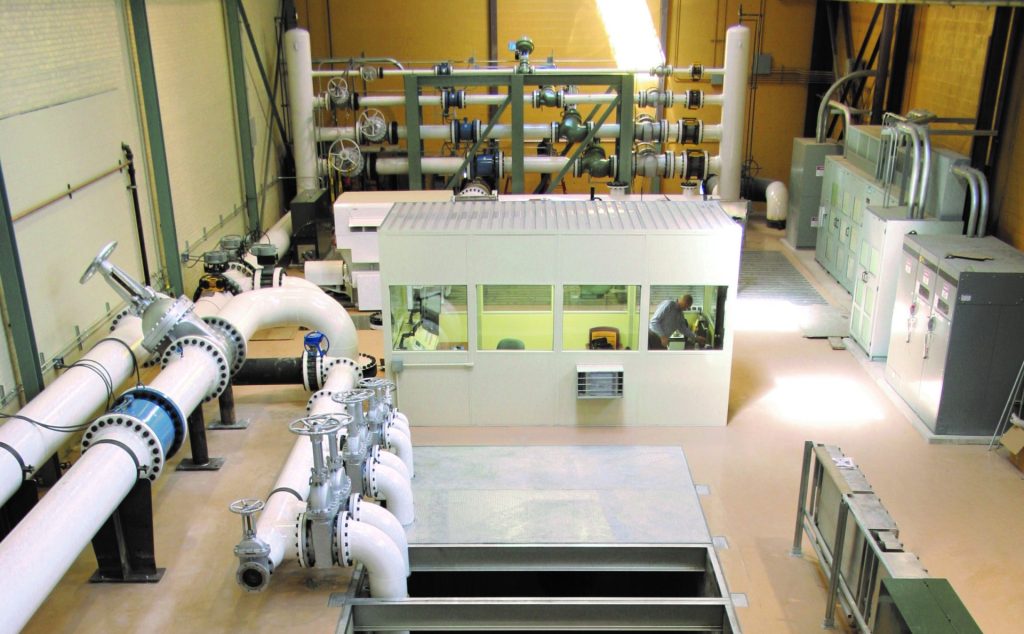
- Where required, hydraulic components are tested in Hydro’s Performance Test Lab
Case Study:
Hydro Rocky Mountain has a long history of doing repairs on hydro-test pumps for a local steel mill. When a pump returned to the shop for one of its increasingly regular repairs, Hydro suggested that a material upgrade on the casing would not only save the customer money on the current repair but decrease the cost of future repairs.
The customer agreed, and Hydro Rocky Mountain worked with Hydro Parts Solutions to cast a new casing for the pump in carbon steel, upgrading the material from its original bronze casing.
Parts Problems? Let's Connect.
Hydro pays particular attention to evaluating what causes a part to fail as well as defining the critical characteristics required to minimize the possibility of failure in newly manufactured parts.
Your questions and comments are important to us. Submit a form below, or reach us by phone and we’ll be in touch as soon as possible.