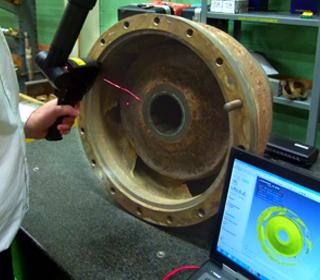
Hydro uses state-of-the-art technology to solve parts needs.
Hydro uses state-of-the-art technology to solve parts needs.
A nuclear power plant required field service support for their high energy multi-stage diffuser barrel pump when a feeler gage became lodged inside the pump element. The station had been experiencing a problem with a lube oil pump and the decision was made to flush the lube oil lines. During this process, the plant’s maintenance team recognized that the charge pump’s inboard pump bearing housing dowels had been bent and the rotor was not properly centered on the inboard end. As Murphy’s Law dictates, “anything that can go wrong, will go wrong”. While the rotor was being centered, a feeler gauge that had been left in the element broke off and became stuck in the inboard end at the first-stage wear ring between the inboard impeller shroud and cover wall.
Picture above shows where feeler gage had become lodged in the element.
The rotor had shuttled and rotated a considerable amount during the original attempt to remove the broken remnant. The station contacted a reliable pump aftermarket service provider who had a highly-skilled field service team with the knowledge and experience to provide support. The station wanted to get this pump back online quickly and asked the field service team to work around the clock to retrieve the broken material and complete the pump assembly. The field service team collaborated with the station’s maintenance team to resolve the issues and get the pump back into service.
A bore scope was used to confirm the piece could not be easily extracted without removing the element. The Technical Field Advisor submitted to the station an Element Removal and Installation Procedure which defined the steps for retrieving the broken feeler gage and properly installing the element back into the barrel. Upon approval of the procedure, day and night shifts were scheduled to resolve the issues.
NAES endeavors to form relationships with industry leading companies that provide value to plant owners through preferential services, scheduling priority, and cost concessions commensurate with the volume of business that a given vendor conducts with the NAES operated fleet. The impact of this initiative is evident to almost all NAES operated plants with plant owners benefiting from significant reductions in operating expenses and improved service response.
John Brewster, NAES President and CEO, said “NAES is focused on safety, compliance, maintenance of asset value, and performance. Performance takes on dimensions of attainment of technical performance goals, adherence to operating plans and budget, cost-effectiveness, and owner satisfaction. Our preferred vendor agreements are designed to deliver the value to help us deliver the best performance that enhances an owner’s return.” He added that “the addition of Hydro to this program demonstrates their commitment to support our efforts to deliver a superior service experience.”